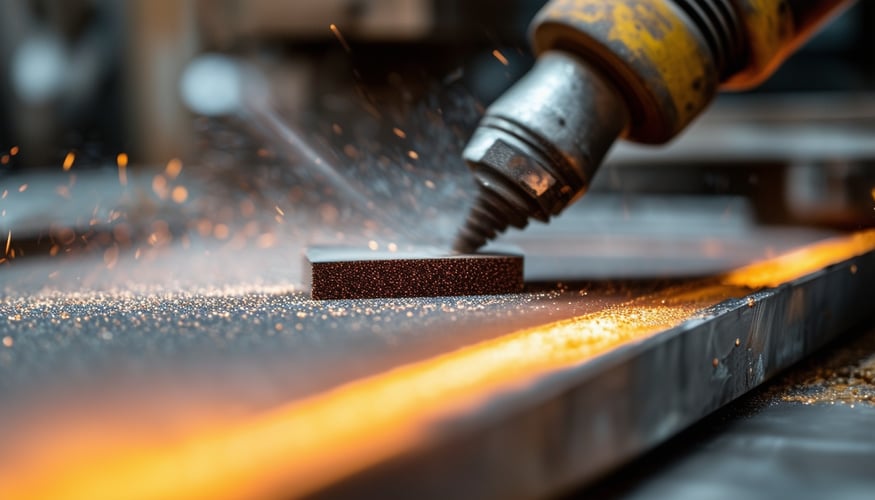
Table of Contents
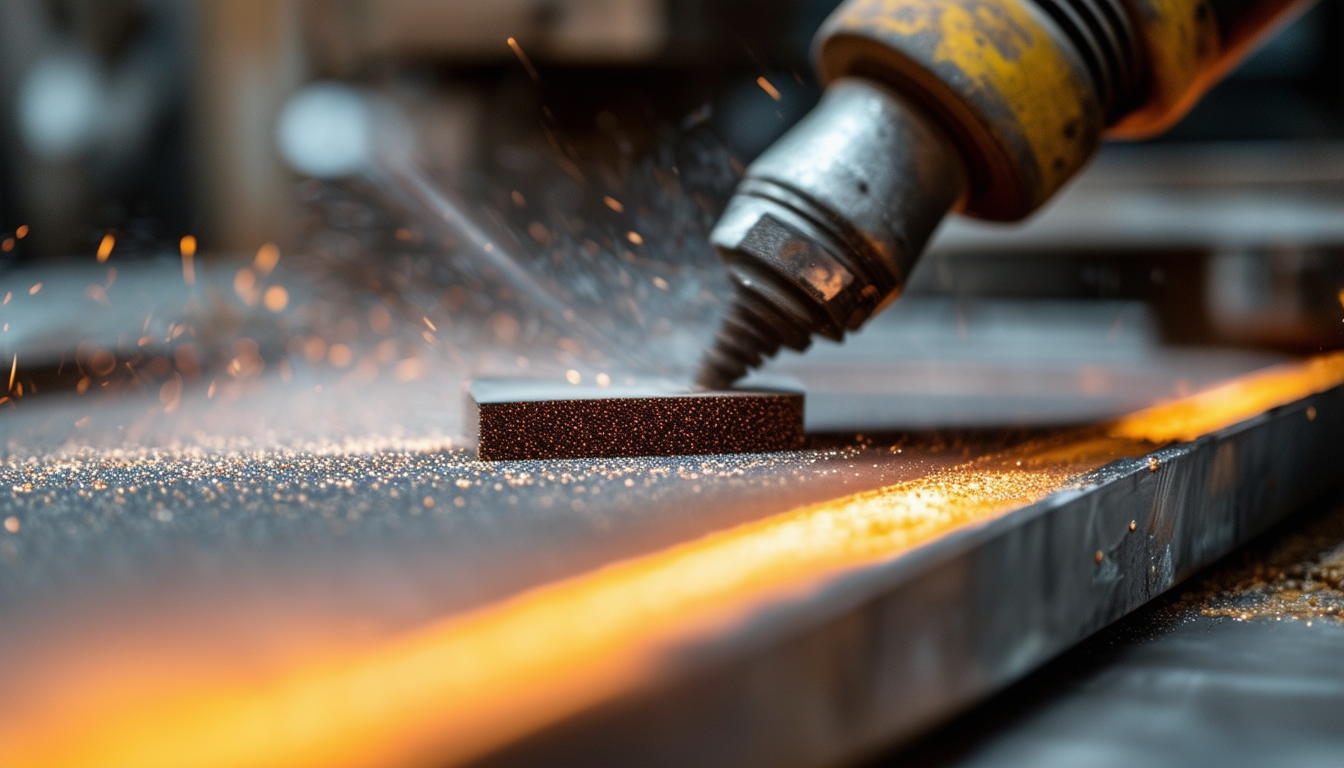
Unlock the potential of your metalworking projects with the right abrasive tools. Discover the essential techniques and tools that can transform raw metal into a masterpiece.
Understanding the Basics of Abrasive Tools
Abrasive tools are essential in the manufacturing industry, especially for metalwork. These tools use materials with a coarse surface to grind, smooth, or polish other surfaces, typically metals. The abrasive action is achieved through the friction created between the abrasive material and the metal surface, effectively removing unwanted material and shaping the metal.
The primary components of abrasive tools include the abrasive grains, bonding material, and the backing or substrate. The abrasive grains are the cutting elements, while the bonding material holds these grains together. The backing provides support and structure to the abrasive product. Understanding these components helps in selecting the right abrasive tool for your specific metalworking needs.
Common Types of Abrasive Tools in Metal Work
There is a wide variety of abrasive tools used in metalwork, each designed for specific tasks and applications. Some of the most common types include:
1. **Grinding Wheels**: Ideal for heavy-duty grinding and cutting operations, grinding wheels come in various sizes and abrasive materials to suit different metals and applications.
2. **Abrasive Belts**: Used in belt sanders, these are great for surface preparation, deburring, and finishing tasks. They offer a continuous supply of fresh cutting edges as they wear down.
3. **Abrasive Discs**: Commonly used in angle grinders, these discs are perfect for cutting, grinding, and polishing metal surfaces. They come in various grit sizes and materials.
4. **Sanding Sheets**: These are versatile and can be used manually or with power tools for sanding and finishing metal surfaces.
5. **Abrasive Flap Wheels**: These tools are excellent for blending, deburring, and finishing due to their flexible and conformable nature.
Selecting the Right Abrasive Tool for Your Project
Choosing the right abrasive tool for your metalworking project is crucial for achieving the desired results. Consider the following factors when making your selection:
1. **Material Type**: The type of metal you are working with will determine the appropriate abrasive material. For instance, aluminum oxide is suitable for ferrous metals, while silicon carbide is better for non-ferrous metals.
2. **Grit Size**: The grit size of the abrasive tool affects the finish and material removal rate. Coarser grits (lower numbers) remove material quickly but leave a rough finish, while finer grits (higher numbers) provide a smoother finish.
3. **Tool Compatibility**: Ensure that the abrasive tool is compatible with your equipment, whether it is a grinder, sander, or other power tools.
4. **Application**: Different tasks such as cutting, grinding, polishing, or finishing require specific types of abrasive tools. Match the tool to the task for optimal performance.
Safety Measures When Using Abrasive Tools
Safety is paramount when working with abrasive tools due to the high speeds and potential hazards involved. Follow these safety measures to ensure a safe working environment:
1. **Protective Gear**: Always wear appropriate personal protective equipment (PPE) such as safety goggles, gloves, ear protection, and dust masks to protect against flying debris, noise, and dust.
2. **Tool Inspection**: Before use, inspect the abrasive tool for any signs of damage or wear. Do not use damaged tools as they can break apart and cause injuries.
3. **Proper Handling**: Handle abrasive tools with care, and ensure they are securely mounted on the equipment. Follow the manufacturer's guidelines for installation and use.
4. **Work Area Safety**: Keep the work area clean and free of flammable materials. Ensure good ventilation to avoid the buildup of dust and fumes.
Maintaining and Prolonging the Life of Abrasive Tools
Proper maintenance of abrasive tools not only extends their lifespan but also ensures consistent performance. Here are some tips for maintaining your abrasive tools:
1. **Regular Cleaning**: Clean abrasive tools regularly to remove dust, debris, and buildup that can reduce their efficiency. Use a brush or compressed air to clean the tools.
2. **Storage**: Store abrasive tools in a dry, cool place to prevent moisture and temperature-related damage. Keep them in their original packaging or hang them on racks to avoid deformation.
3. **Usage Practices**: Use the tools within their recommended speed and pressure limits. Overloading or excessive pressure can cause premature wear and damage.
4. **Rotation**: Rotate the use of multiple abrasive tools to ensure even wear and prolong their overall lifespan.