Superhard Materials and Advanced Cutting Technology: From Carbide to Next-Generation Tool Evolution and Applications
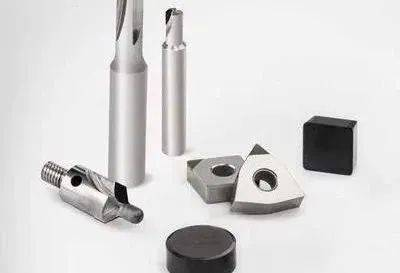
Table of Contents
As early as 1926, German researchers successfully developed carbide, which then evolved into innovative tools coated with carbide, becoming an indispensable cutting tool for over 80 years. Additionally, tools such as PCD and PCBN play significant roles in the cutting field.
In recent years, experts and scholars have focused on two novel superhard material technologies: new PCBN grades for high-speed machining of cast iron, diamond-coated carbide for drilling CFRP, and BL-PCD face milling for direct carbide milling. These innovative technologies and tools have opened new possibilities for machining, driving constant development in the materials processing field.
- CBN for High-Speed Milling of Cast Iron
PCBN sintered bodies come in two types: one where CBN particles are bonded with a binder, and another where a small amount of binder material bonds the CBN particles together. The former has excellent wear resistance and is used for hardened steel cutting, while the latter, with a higher CBN content and good thermal conductivity, is used for cast iron, heat-resistant alloys, and PM parts. - Diamond-Coated Tools for CFRP Processing
A notable feature of composite materials is their controlled mechanical characteristics by combining matrix and reinforcement materials. Carbon Fiber Reinforced Plastic (CFRP) is widely used in industrial machinery such as cars, helicopters, medical devices, and railway vehicles due to its superior tensile strength, specific gravity, and corrosion resistance. In aerospace, CFRP is a foundational structural material that reduces the weight of aircraft bodies, improving fuel efficiency and lowering maintenance costs. - Direct Milling of Carbide
In mold preparation processes, to improve mold accuracy, coated carbide end milling is typically used for direct milling. As manufacturers demand higher hardness for molds, polycrystalline diamond (PCD) tools, diamond-coated carbide tools, and single-crystal diamond (SCD) tools have emerged for direct milling of hard materials.
However, traditional PCD tools lack the hardness required for direct milling of carbide molds, and SCD lacks strength. The sharpness of both PCD and diamond-coated tools is also insufficient. This led to the development of binderless nano-polycrystalline diamond (BL-PCD). BL-PCD has higher hardness than PCD and SCD, and its sharpness exceeds that of both PCD and diamond-coated tools, making it ideal for direct milling of carbide molds, especially for finishing operations.