A Review of Research on the Ultimate Semiconductor Material — Diamond
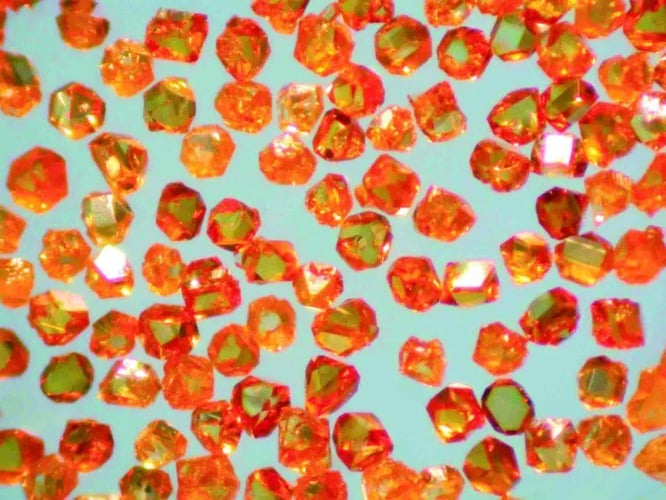
Table of Contents
Introduction
The excellent physical and chemical properties of diamond allow its extensive application in various fields. Diamond is an indirect bandgap semiconductor material with a bandgap width of approximately 5.2 eV, a thermal conductivity of up to 22 W/(cm•K), and room temperature electron and hole mobility reaching 4500 cm²/(V·s) and 3380 cm²/(V·s), respectively, far exceeding those of third-generation semiconductor materials like GaN and SiC. Therefore, diamond holds broad application prospects in high-power electronic devices operating at high temperatures and high-frequency microwave devices. Additionally, due to its large exciton binding energy (80 meV), diamond can achieve strong free exciton emission at room temperature (with a luminous wavelength of approximately 235 nm), showing great potential for fabricating high-power deep ultraviolet light-emitting diodes. It also plays an important role in the development of extreme ultraviolet, deep ultraviolet, and high-energy particle detectors. Although there are many challenges in the growth of semiconductor diamond materials and the development of devices, it is predicted that the applications of semiconductor diamond materials and devices are likely to bring significant technological transformations in the near future.
The preparation methods for single crystal diamonds mainly include High-Pressure High-Temperature (HPHT) method and Chemical Vapor Deposition (CVD) method. The single crystal diamonds produced using the HPHT method with metal catalysts inevitably incorporate a considerable amount of metal impurities, which makes it difficult to meet the requirements of semiconductor devices. The CVD method mainly includes Hot Wire CVD, DC Jet CVD, DC Discharge CVD, RF CVD, and Microwave Plasma CVD (MPCVD), among which MPCVD has many advantages and is currently recognized as the best method for preparing high-quality single crystal diamonds. The MPCVD reaction chamber has no internal electrodes, eliminating the problem of electrode contamination, and the microwave power can be continuously and smoothly adjusted, with high microwave energy conversion efficiency and high plasma density. The stable conditions in the reaction chamber provide MPCVD with unique advantages in producing high-quality semiconductor diamond. Semiconductor devices have high quality requirements for materials, as the introduction of defects can severely affect the electrical and optical properties of semiconductor materials. Therefore, high-quality diamond materials are key to ensuring their semiconductor applications. Additionally, for the growth of single crystal diamond substrate materials, high growth rates and large crystal sizes are also required. Achieving the semiconductor function of diamond necessitates effective doping to endow it with good n-type or p-type conductive properties. However, current MPCVD methods for preparing single crystal diamonds still struggle to meet the requirements for high-performance semiconductor devices in terms of growth rates, material sizes, crystal sizes, and semiconductor doping.
Preparation of Semiconductor Single Crystal Diamond Substrates
Expanding the crystal size of CVD diamond substrates and achieving rapid growth of single crystal diamonds are prerequisite conditions for preparing high-quality, large-size semiconductor diamond materials.
MPCVD methods for producing large-area single crystal diamonds mainly include three approaches: repeated growth, three-dimensional growth, and mosaic growth. The repeated growth method involves removing the sample after each growth interval, polishing and cleaning the growth surface, and then continuing the growth. This process is repeated multiple times to achieve the growth of large-sized diamonds. The purpose of polishing the sample surface is to remove the steps and polycrystalline structures formed on the surface of the epitaxial layer, ensuring continued growth. Studies show that the repeated growth method can achieve a thicker single crystal in vertical growth, but it is challenging to effectively achieve lateral epitaxy, thus limiting the expansion of single crystal diamond area. The three-dimensional growth method requires combining the repeated growth method; first, a certain thickness is grown on the (100) surface of the substrate using the repeated growth method, and after polishing the sample surface, growth is performed on the side (010) surface. This process is repeated multiple times to achieve the deposition of large-area single crystal diamonds. Similarly, the three-dimensional growth method also faces the problem of gradually declining crystal quality with increasing interruption frequency. Moreover, the low efficiency and high costs brought about by multiple growths and surface treatments are also significant issues. The mosaic growth method, also known as the stitching method, is a technique that involves assembling multiple small diamond substrates of consistent size, thickness, and crystal orientation into a larger substrate, on which large-area single crystal diamonds are deposited. It is crucial to ensure that the crystal orientations of the different small substrates match, as any deviation will directly affect the quality of the epitaxy. Thus, a key factor in the mosaic growth method is how to obtain small substrates with highly consistent crystal orientations. Compared to repeated growth and three-dimensional growth methods, the mosaic growth method has obvious advantages in producing large-area single crystal diamonds, not only providing a larger area but also ensuring better crystal quality (except at the seams). However, this method also has drawbacks. Since it involves the stitching of small substrates, achieving a perfect match between the small substrates is challenging. As a result, defects inevitably form at the junctions of the small substrates, which can even lead to cracking. H. Yamaha and others used the mosaic growth method to produce large-area single crystal diamonds. When the small square substrates were stitched together in parallel, significant cracks appeared in the epitaxial layer. However, when the edges of the small substrates were treated to form a certain tilt angle, the resulting diamond epitaxial layer exhibited a smooth and crack-free growth surface. The mosaic growth method also has a problem due to the large deposition area, as the growth conditions at different positions on the substrate can vary significantly, ultimately leading to uneven quality of the grown single crystal diamonds. This necessitates optimizing the structure of the reaction chamber to achieve a more uniform distribution of the plasma ball, thereby enhancing the uniformity of large-area single crystal diamond substrates.
Y. Mokuno and others utilized a 10 mm x 10 mm single crystal diamond seed crystal as a substrate, successfully achieving epitaxy of a single crystal diamond measuring 12 x 13 x 3.7 mm³ and weighing 4.65 carats using the MPCVD method in conjunction with ion implantation and exfoliation techniques through repeated growth on different sides. This size has far exceeded the maximum size of single crystal diamonds that could be commercially synthesized using the HPHT method at that time. However, this method is constrained by various processing factors, and the actual operational process is quite complicated, so three-dimensional expansion growth is not an optimal method for producing large single crystals. In contrast to three-dimensional growth methods, the mosaic method is a faster way to obtain large-sized single crystals (as shown in Figure 2) and has a simpler operational process. H. Yamada and others successfully synthesized multiple single crystal diamond plates measuring up to half an inch using ion implantation and exfoliation techniques, which had the same crystal characteristics as the seed crystals. They then selected the better ones to form a mosaic substrate and conducted diamond epitaxial growth. They again used exfoliation techniques and repeated deposition to finally synthesize large-size single crystal diamond wafers. Currently, this size is still some distance away from the size required for diamond semiconductors, which is generally believed to need to reach two inches to be applicable to the development of semiconductor devices. Overall, the mosaic stitching technology provides an effective pathway for the growth of large-sized single crystal diamonds, and with advancements and improvements in growth processes, the issues related to the surface quality of diamond growth caused by stitching interfaces will gradually be resolved.
As of now, due to high production costs, the application of single crystal diamond in the market is limited. Reducing production costs will significantly broaden the application value of diamonds, and the only way to lower costs is to improve efficiency to achieve mass production. Since Asmussen and others successfully realized the simultaneous growth of nearly a hundred seeds using the 915MHz MPCVD method, the growth of large quantities of single crystal diamonds has garnered increasing attention from researchers. To enhance growth rates, a multi-wafer growth method can be employed.
- Preparation of High-Quality Semiconductor Single Crystal Diamond
Growing high-quality diamond epitaxial layers on single crystal diamond substrates is a necessary condition for device fabrication; this epitaxial layer typically serves as the functional region of the device (for example, the active region of a light-emitting diode). Unlike substrate preparation, this epitaxial layer has a small thickness but requires higher material quality. Therefore, its growth conditions differ significantly from those used for high-speed large-area growth aimed at substrate fabrication. As the epitaxial layer is intended to achieve device functionality, it must possess excellent electrical and optical properties, as well as a smooth epitaxial growth surface, striving for atomically flat surfaces while minimizing surface impurities, dislocation defects, and the formation of polycrystalline materials. Consequently, the growth conditions for high-quality single crystal diamonds generally adopt low-speed growth, low methane-to-hydrogen gas flow ratios, and low microwave power, allowing for the slow and stable deposition of diamond. While using higher microwave power and slightly increasing the methane-to-hydrogen flow ratio can effectively enhance growth rates, it may somewhat reduce the flatness of the single crystal diamond surface but can maintain high crystal quality. Compared to the (001) plane, the (111) plane more readily produces twin crystals, stacking faults, and other defects, making it challenging to achieve a smooth surface. However, the (111) plane diamond is more conducive to P-type doping, thus the preparation of high-quality (111) plane single crystal diamonds holds certain significance for device applications.
- Research on Single Crystal Diamond Doping
Doping intrinsic single crystal diamonds is key to realizing diamond semiconductor devices, as they exhibit electrical insulation due to their large bandgap. Achieving P-type and N-type doping in diamonds is crucial for the research of diamond semiconductor devices. Due to the dense lattice structure and small lattice constant of diamond, most atoms find it challenging to be incorporated into the diamond lattice. Currently, the only P-type dopant realized for diamond is boron (B), while phosphorus (P) serves as the N-type dopant. The primary doping methods for diamonds include diffusion, ion implantation, and CVD in-situ doping. The diffusion method involves introducing impurities into diamond under vacuum and high-temperature conditions; this method is limited by diffusion coefficients and equilibrium concentrations, resulting in a low concentration of incorporated dopants. The ion implantation method directs high-energy impurity ion beams onto diamonds, which may disrupt the diamond's lattice structure and even cause graphite formation on the diamond surface. The CVD in-situ doping method incorporates appropriate doping gases into the reaction gas, allowing impurities to enter the diamond lattice through deposition. CVD in-situ doping features uniform and stable impurity incorporation without damaging the diamond's lattice structure. For potential dopants like lithium (Li), nitrogen (N), and aluminum (Al), reliable experimental data is still lacking, leading scientists to simulate analyses of these elements through theoretical calculations. For Li atoms in diamonds, two forms of existence are possible: substitutional and interstitial. The formation energy of interstitial Li atoms in diamonds is 1.74 eV lower than that of substitutional Li atoms, thus indicating that interstitial Li atoms are the most stable form in diamonds, with impurity energy levels approximately 0.143 eV above the conduction band minimum, exhibiting donor characteristics. Similarly, sodium (Na) doping in diamonds also presents both substitutional and interstitial forms, with substitutional Na atoms having a formation energy 2.87 eV lower than interstitial Na atoms. Therefore, it is considered that Na atoms in diamonds may predominantly exist in substitutional form. Aluminum (Al) presents a donor impurity energy level in diamonds, located approximately 0.4 eV below the valence band maximum, which is a deeper level. Nitrogen (N) atoms, being relatively small in radius, can easily be incorporated into the diamond lattice. First-principles calculations of N-doped diamond surfaces reveal that substitutional N can exhibit both N-type and P-type conductivity based on different bonding situations. However, when exhibiting P-type conductivity, the formation energy is significantly high, making it difficult to achieve, as N introduces deep energy levels below the conduction band by 1.7 eV, categorizing it as a deep donor level with no conduction band electrons available. Compared to N impurities, the formation energy of substitutional P in diamonds is lower, with impurity energy levels closer to the conduction band minimum at 0.58 eV, currently being the only donor element that can demonstrate N-type conductivity experimentally.
The P-type doping of co-doped diamonds can be relatively stable, whereas N-type doping still faces challenges, including deep energy levels and poor reproducibility, even when using phosphorus (P). Consequently, researchers have begun to explore achieving N-type doping in diamonds through co-doping methods. Group VI elements (such as sulfur) may display N-type conductivity in diamonds. Studies show that co-doping with boron (B) and sulfur (S) can enhance the electronic conductivity of diamonds. The formation energy of co-doping is lower than that of single doping with group VI elements, indicating that the presence of B facilitates the incorporation of group VI elements. As donor centers, group VI elements release electrons, allowing the co-doped system to exhibit N-type conductivity. The presence of B can potentially capture electrons released by donor centers, thereby somewhat reducing the N-type conductivity of diamonds. Boron is currently the only element that can effectively realize P-type doping in diamonds. With a relatively small atomic radius, B can easily be incorporated into the diamond lattice. It contains three valence electrons and exists as an acceptor element in diamonds, with an activation energy of 0.37 eV, categorizing it as a deep level with low ionization efficiency at room temperature. Research also indicates that higher microwave power can significantly enhance the doping efficiency of B. The B doping of diamonds is related to the tilt angle of the substrate, with studies showing that the tilt angle of the diamond substrate can significantly impact the doping of B in diamonds. Increasing the tilt angle can effectively raise the number of atomic steps on the growth surface, allowing B atoms to be incorporated more effectively into the diamond lattice within a certain angle range. The doping efficiency of B is temperature-dependent; appropriately raising the growth temperature is beneficial for doping, resulting in higher doping levels and ionization effects.
Furthermore, diamond surfaces also feature hydrogen-terminated P-type doping. Field-effect transistors with hydrogen-terminated P-type surface channels exhibit high breakdown voltages and low reverse leakage currents; however, these surface channels suffer from poor thermal and chemical stability. Despite the current inadequacies in P-type doping of diamonds, characterized by deep acceptor levels, low ionization efficiency, and slow growth rates, significant progress has been made in devices based on P-type diamonds. P-type diamonds can be utilized in the fabrication of field-effect transistors and Schottky diodes, among other devices. N-type doping in diamonds is more challenging than P-type doping, with potential donor elements including group I elements (Li and Na), group V elements (N, P, As, and Sb), and group VI elements (S). The theoretical activation energies of Li and Na as interstitial atoms are 0.1 eV and 0.3 eV, respectively, indicating their potential as donors in diamonds. However, experimental results show that Li and Na-doped diamonds exhibit high resistance and low ionization rates. Additionally, the solubility of Li and Na in diamonds is quite low, making it difficult to incorporate them into the diamond lattice. Nitrogen (N) atoms have a small radius, similar to carbon (C) atoms, making them relatively easy to incorporate into the diamond lattice.
- Major Existing Issues
Nevertheless, there are still several prominent issues in the growth of semiconductor-grade diamond materials. To meet the requirements for semiconductor device applications, broader and deeper research is needed: First, the single crystal growth for semiconductor applications heavily relies on homoepitaxy. The limited size of homoepitaxial substrates presents a bottleneck. Although the splicing method can produce substrates around 2 inches, it is highly inefficient and costly, making mass supply unfeasible. Second, the quality of single crystal diamond materials requires further improvement. While good diamond materials can be grown under slow and optimized conditions, there remains a significant gap compared to current SiC and GaN materials, necessitating breakthroughs in material growth theory and technology. Third, doping remains the greatest obstacle for semiconductor applications. Further in-depth experimental work is needed on B-doping and P-doping diamond materials to enhance room-temperature carrier concentrations and reduce resistivity.
As of now, the main issues faced in the mass growth of single crystal diamonds are: First, the limitations of deposition equipment. Currently, the rated power of equipment on the domestic market generally does not exceed 6 kW, which restricts the effective deposition area and deposition rate of single crystal diamond growth, directly impacting growth efficiency. Second, the quality and yield of mass growth are critical. Unlike single-piece diamond growth, which can ensure quality through strict control of the growth process, multi-piece growth faces challenges in maintaining growth quality due to differences in surface quality and placement. This issue is also significantly related to the equipment's performance (the state, shape, and size of the plasma ball generated by the equipment), substrate platform, and process design.
6.The Ultimate Semiconductor Material: Diamonds Have Significant Advantages
We are now in an era where information is beginning to explode, and this explosion of information is thanks to silicon crystal semiconductors. However, in terms of functionality, silicon crystals are not the best semiconductors. Taking transistors used for radio frequency power amplifiers as an example, an important functional indicator is the output power of the load. To increase this power, it is necessary for the product of the square of the frequency and the load impedance of the crystal to be as large as possible. Based on this indicator, diamonds are 8,200 times better than silicon crystals, 500 times better than gallium arsenide, and 8 times better than silicon carbide. The table presents several semiconductor materials with superior performance compared to silicon crystals and their properties. The data in the table clearly indicates that the overall performance of diamond semiconductors far exceeds that of silicon crystals.
Diamond semiconductors not only operate at high speeds but also exhibit excellent temperature resistance. Silicon wafers can only withstand temperatures below 300°C, while gallium arsenide wafers can tolerate temperatures not exceeding 400°C. In contrast, diamonds can be heated to nearly 700°C without damage. Moreover, diamond has the highest thermal conductivity of all materials, being 30 times faster than silicon crystals. When operating, high-power diamond semiconductors can dissipate heat without the need for additional cooling devices, making them ideal materials for integrated circuits.
For diamond semiconductors to become mainstream, they will need to wait until the end of silicon crystal technology. Only when silicon reaches its inherent limits will the superior performance of diamond semiconductors be recognized, allowing them to develop into commercial products. At that time, diamond semiconductors will further unify the industry, elevating human civilization to new heights and ushering in an eternal diamond age.
Although diamond semiconductors currently face challenges, their long-term prospects remain positive. The golden age of semiconductors began with germanium, transitioned through silicon, and may eventually be taken over by silicon carbide. Silicon carbide has a diamond-like structure, but half of its atoms are carbon, making it a sort of "half diamond." Silicon carbide should be seen as a transitional product as we move from the silicon era to the diamond semiconductor era.
Diamonds will undoubtedly become the mainstream material for future semiconductors. Observing the shifts in semiconductor eras reveals a progression through the central group of the periodic table (Group 14), traversing germanium, silicon, silicon carbide, and ultimately carbon (i.e., diamond) at the pinnacle of the periodic table. There are no elements above carbon; thus, once diamonds dominate, there will be no further changes in the semiconductor landscape. If no materials can replace diamonds in the future, the phrase “Diamond is Forever” may indeed become prophetic.