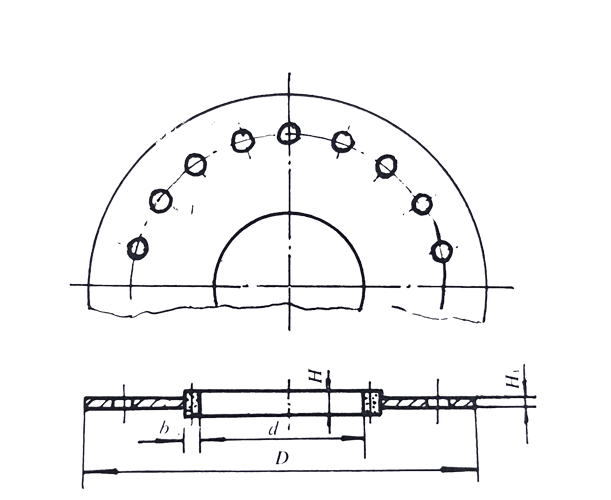
Table of Contents
1. Cabezal de rectificado galvánico
La forma de los cabezales de rectificado incluye formas cilíndricas y varias formas especiales (como trapezoidal, ovalada, cuadrada, cónica, en forma de llama, etc.). Los diámetros oscilan entre 0,2 mm y 15,7 mm. El vástago se procesa mediante torneado. La excentricidad radial debe cumplir estrictamente los requisitos pertinentes.
Figura 1 Cabezal de rectificado galvánico
1.1 Flujo del proceso
Procesamiento del alambrón → Inspección del alambrón → Nivelación mecánica → Desengrase químico (30-60 minutos) → Aclarado con agua caliente → Aclarado con agua fría → Aclarado con agua fría → Aplicación de pintura aislante → Soldadura de alambre → Instalación de la fijación → Desengrase electrolítico → Aclarado con agua fría → Aclarado con agua fría → Grabado con ácido clorhídrico concentrado (1 minuto) → Aclarado con agua fría → Activación química o electroquímica con ácido sulfúrico diluido (0.5-1 minuto) → Entrada eléctrica directa en el tanque para el chapado en vacío (10 minutos) → Método de incrustación en arena → Espesamiento (movimiento catódico) → Enjuague con agua fría → Limpieza → Desengrasado y desoxidación → Enjuague con agua caliente → Enjuague con agua fría → Enjuague con agua fría → Electrodeposición de la capa brillante (Ni, aleación NiCo o Cu-Ni-Cr) → Enjuague con agua fría → Eliminación del hidrógeno → Inspección de calidad.
1.2. Proceso clave
1.2 Puntos clave del proceso
1.2.1 Accesorio de aplicación de arena El accesorio de aplicación de arena utiliza un accesorio tipo ranura con una ranura de arena recta hecha de vidrio orgánico poroso, forrado con tela de nylon. Se insertan varios cabezales de rectificado uno al lado del otro en la ranura de arena. El método de trabajo óptimo consiste en disponer los extremos de trabajo hacia arriba para la aplicación de arena.
Figura 2 Dispositivo de aplicación de arena tipo marco
El accesorio de tipo marco está hecho doblando alambre de cobre de φ3mm en un marco cuadrado, colocado sobre una placa de soporte de plástico. Durante la aplicación de arena, el cabezal de esmerilado se coloca plano y se suelda al marco de cobre (véase la figura 2). Tras la aplicación de arena en un lado, se gira 180 grados para aplicar arena en el lado inverso. 1.2.2 Correspondencia entre el tamaño del grano abrasivo y el diámetro del cabezal esmerilador Consulte la Tabla 1 para obtener información detallada sobre la correspondencia entre el diámetro del cabezal esmerilador y los tamaños de grano abrasivo adecuados.
1.2.3 Engrosamiento
Después de ser retirado de la fijación, el cabezal de esmerilado se suspende en el tanque de revestimiento para el espesamiento hasta que el espesor alcanza aproximadamente el 80% del tamaño de grano (es decir, enterrado 80%). Otros puntos clave se muestran en la Tabla 2.
Tabla 2 Puntos clave del proceso de galvanoplastia para productos de materiales superduros
1.2.4 Revestimiento de la capa brillante
Después del proceso de espesado, se elimina el material aislante. Después de desengrasar y desoxidar, el cabezal de rectificado y su biela se electrochapan con una capa decorativa protectora.
Capa brillante.
Las limas electrochapadas
Las limas electrochapadas
Las limas electrochapadas vienen en tipos manuales y mecánicos, con más de cien especificaciones diferentes. A nivel nacional, un juego típico de limas surtidas incluye de 10 a 12 formas diferentes (véase la Tabla 3). El tamaño del grano abrasivo se determina en función de los requisitos del usuario para el acabado de la superficie de mecanizado, y suele oscilar entre 100/120 y 270/325.
Tabla 3.
Tabla 3
2.1 Flujo del proceso
Aclarado con agua → Conexión de cables → Tratamiento de aislamiento → Instalación de fijaciones → Desengrase electroquímico → Procesado y conformado de metal en bruto en caliente → Tratamiento mecánico superficial → Desengrase químico alcalino → Aclarado con agua caliente → Aclarado con agua fría → Aclarado con agua fría → Aclarado con agua fría → Grabado → Prechapado → Aplicación de arena → Espesado → Aclarado con agua fría → Limpieza y recorte → Limpieza de desengrase y desoxidación → Chapado brillante → Aclarado con agua fría → Secado → Inspección → Impresión de marca comercial → Embalaje → Almacenamiento.
2.2 Puntos clave del proceso
2.2.1 Sujeción del aislamiento
La pieza en bruto de la lima se conecta al alambre, y las superficies que no funcionan se aíslan con película o tubos de plástico. A continuación, se instala en una fijación especial.
2.2.2 Grabado
Primero, la lima se graba en una solución de ácido clorhídrico de 150-300 g/L durante 1-2 minutos, seguido de una limpieza y, a continuación, un grabado químico débil en una solución de ácido sulfúrico diluido al 3%-5% o un grabado electroquímico débil en una solución de ácido sulfúrico diluido al 1%-3% con una corriente de 5-10 A/dm² durante varios segundos a medio minuto.
2.2.3 Grabado químico débil
La lima se graba en una solución de ácido sulfúrico diluido al 1%-3% con una corriente de 5-10 A/dm² durante varios segundos a medio minuto.
2.2.3 Galvanoplastia previa
Después del grabado, la lima se carga directamente y se somete a un pre-chapado durante 10-20 minutos, con la corriente (ik) a aproximadamente 1 A/dm².
2.2.4 Aplicación de arena
Para el método de caída de arena, la pieza en bruto de la lima se coloca en una cavidad de molde de vidrio orgánico que contiene abrasivo y electrolito. El molde se agita para suspender el diamante y luego se estabiliza para la aplicación de arena. Se requieren múltiples rotaciones para aplicar arena desde varios ángulos (véase la Tabla 27). La corriente de aplicación de la arena no debe ser superior a 1,2 A/dm², siendo el tiempo de aplicación de la arena de 8,7 y 5 minutos para los granos de tamaño 100, 120 y 150, respectivamente. Para el método de incrustación de arena, la lima en bruto se coloca en un soporte especial (como se muestra en la figura 3, el soporte tipo marco), y se esparce diamante uniformemente sobre la lima en bruto y sus alrededores. La arena se aplica una vez (reposición de la arena). Se aplica la corriente para incrustar la arena, después se gira el dispositivo 180 grados, y se aplica una corriente de 0,2-0,5 A/dm².
2.2.5.2. Aplicación del diamante en la pieza en bruto
2.2.5 Espesado
Durante el regrueso, deben tomarse precauciones para evitar que el filo de corte quede excesivamente chapado o chamuscado. Deben utilizarse cátodos protectores o placas aislantes como medidas de apantallamiento. En el caso de las limas surtidas manuales, el espesor de la capa galvánica suele alcanzar el 60%-70% del tamaño medio del grano. Disco de corte circular interior de diamante galvánico Se trata de una herramienta de corte utilizada para cortar materiales valiosos, fabricada mediante galvanoplastia de una capa de diamante fino en el borde del diámetro interior de un disco fino de acero inoxidable. La forma es la que se muestra en la figura 3. Los tamaños de grano habituales son 270/325, 325/400 o micropolvo 36-54. Las especificaciones típicas (mm) incluyen el diámetro interior d83-130, el diámetro exterior D206-300, H0,2-0,3, H1 0,1-0,2 y b0,5-2,03.
Figura 3 Cuchilla de corte de diámetro interior
3.1 Flujo del proceso: Desengrase químico de la base → Carga de los discos → Pulido electrolítico → Limpieza → Tratamiento de corriente inversa en el baño de metalizado → Metalizado de la capa base → Metalizado de la capa de diamante (incrustación y engrosamiento del grano) → Desmontaje y limpieza → Secado → Marcado → Almacenamiento
3.2 Puntos clave del proceso:
3.2.1 Carga de los discos: Varios sustratos de discos delgados y placas de vidrio orgánico se colocan alternativamente en un molde de vidrio orgánico dedicado, con tela de nylon como revestimiento, y el conjunto se sella con una tapa final. El apriete de los tornillos garantiza un sellado y una conductividad adecuados. La figura 4 muestra un esquema del montaje del disco.
Figura 4 Esquema de la fijación de la cuchilla de corte de diámetro interior
3.2.2 Pulido electrolítico: El pulido electrolítico elimina la densa película de óxido de la superficie de acero inoxidable mediante disolución electroquímica y adelgaza el filo de corte. El proceso de pulido consiste en utilizar una solución acuosa de ácido sulfúrico al 50%, con una corriente de 2,5-3 A por disco, durante 1-2 minutos. Después del pulido, se limpia la cavidad interna.
3.2.3 Tratamiento de corriente inversa y capa base de niquelado: La cavidad del molde se llena con una solución de niquelado (NaCl 2200g/L, HCl 125g/L). El sustrato se somete a un tratamiento de corriente inversa durante 1-3 minutos, tras lo cual se cambia la corriente y se aplica la base de níquel durante 3-5 minutos. Las corrientes directa e inversa para cada disco son de 0,13-0,2 A.
3.2.4 Incrustación y espesamiento de la granalla: La cavidad del molde se sustituye por una solución de revestimiento de aleación de níquel-cobalto (véase la Tabla 4), se cargan los ánodos de arenilla y níquel, y se lleva a cabo la incrustación y engrosamiento de la arenilla con una corriente de 0,13-0,2 A por disco. El proceso de incrustación y engrosamiento de la arenilla es el siguiente: se mueve el molde, se coloca horizontalmente en la cara del extremo, se recubre durante 5 minutos y se repite dos veces. A continuación, se coloca el molde verticalmente y se repite el proceso con rotaciones de 60 grados durante 3 minutos cada vez, cubriendo las cuatro caras con diferentes puntos de partida cada vez. Por último, se colocan los discos en posición horizontal, y se recubren las caras anterior y posterior durante 15 minutos cada una (corriente de 50 A por disco).
Tabla 4 Revestimiento
Tabla 4 Fórmula de la solución de metalizado y condiciones del proceso (concentración en g/L)
4. Taladro de núcleo de diamante galvánico
4.1 Taladro de núcleo: La forma de la broca sacanúcleos se muestra en la Figura 5. Las especificaciones se determinan según los requisitos del cliente, generalmente D20-100 mm, D-D1 mm, y h5-20 mm. Los tamaños de grano comunes son 50/60, 60/70, y 70/80.
Figura 5 Taladro de núcleo galvánico
4.1 Flujo del proceso: Montaje → Galvanoplastia simulada → Incrustación de grano → Engrosamiento → Incrustación de grano y engrosamiento repetidos → Retirada del vástago del núcleo → Recorte e inspección inicial → Acabado general (niquelado brillante) → Preparación de la base y del vástago del núcleo → Tratamiento de la superficie antes del galvanoplastia (desengrasado químico e inspección de activación electroquímica)
4.2 Claves del proceso
4.2 Puntos clave del proceso
4.2.1 Eje de núcleo temporal: Se pueden utilizar tres tipos de ejes de núcleo temporales: ejes de núcleo de vidrio orgánico (químicamente chapados con cobre o níquel), varillas de aleación de bajo punto de fusión o formas de núcleo preparadas en base. El diámetro exterior del vástago es el diámetro interior de la perforadora. Estos vástagos de núcleo pueden extraerse por disolución, calentándolos para fundirlos o torneándolos en un torno.
4.2.2 Vástagos de núcleo para perforación de núcleos
4.2.2 Revestimiento de la capa de trabajo: La característica principal es la electrodeposición radial de la capa de trabajo utilizando el vástago de núcleo temporal como base, lo que acorta significativamente el tiempo de metalizado. Tras la activación, el sustrato entra en el baño para el metalizado. La incrustación de la granalla se realiza utilizando el método de la granalla incrustada (véase la Figura 6 para la fijación). El electrolito utiliza la Fórmula 7, con una corriente de 0,2-0,25 A/dm². Tras la eliminación de la arenilla, se realiza el espesado con una corriente de 0,5-1,0 A/dm². El proceso de incrustación de grano y espesamiento se repite hasta que se cumplen las especificaciones requeridas (granallado multicapa).
Figura 6 Dispositivo de incrustación de granos de perforación con corona
5. Rodillo de diamantado galvánico Los rodillos galvánicos son herramientas avanzadas de alta precisión y alta eficiencia. Se utilizan para el reavivado de perfiles complejos de muelas conformadas o directamente para el rectificado de perfiles. Los rodillos tienen varias formas. La figura 7 muestra dos ejemplos. El tamaño de grano depende de los requisitos de procesamiento y puede variar desde 30/35 hasta tamaño de micropolvo.
Figura 7 Esquema de rodillos de diamantado
Rodillos simples.
Los rodillos sencillos pueden fabricarse utilizando el método pulvimetalúrgico o el método de galvanoplastia externa, con una precisión generalmente en torno a 0,02 mm. El proceso de galvanoplastia para rodillos más complejos y de alta precisión es similar al de los productos anteriores mencionados, pero sólo el método de galvanoplastia interna puede garantizar la uniformidad de los granos abrasivos. A continuación se presenta una introducción al método de revestimiento interno. 5.1 Flujo del proceso del método de revestimiento interno: Preparación del molde del cátodo → Tratamiento de la superficie antes del revestimiento → Incrustación de los granos → Espesamiento → Electroconformado → Vertido del núcleo → Mecanizado → Retirada de la cáscara → Recorte de precisión e inspección
5.2 Claves del proceso para el método de revestimiento interno
5.2 Puntos clave del proceso para el método de revestimiento interno
5.2.1 Molde de cátodo: El molde catódico es el molde inverso correspondiente al perfil del rodillo y se utiliza como sustrato temporal para la galvanoplastia. La precisión de la superficie del molde debe ser estrictamente controlada, generalmente ligeramente superior a la precisión del perfil del rodillo (1-2 µm). El molde de cátodo debe someterse a un tratamiento superficial exhaustivo antes de la galvanoplastia.
5.2.2 Incrustación de grano: Los rodillos de alta precisión utilizan el método de incrustación de grano con un dispositivo especial (véase la Figura 8 para el dispositivo de incrustación, y la Figura 9 para la estructura acabada). La densidad de corriente es de 0,2-0,25 A/dm². Después de la primera incrustación de grano, el molde y la fijación se giran 180 grados para una segunda incrustación (grano suplementario).
Figura 8 Dispositivo de incrustación de granalla
Figura 9 Estructura terminada
5.2.3 Espesamiento y electroformación: Utilizando electrolito de Fórmula 6, la densidad de corriente es de 0,5-1 A/dm². El proceso continúa hasta que las partículas de diamante están totalmente incrustadas en la capa de revestimiento, tras lo cual se aumenta la corriente por encima de 1,5 A/dm² para el electroconformado, con un espesor de 2-5 mm. Este proceso puede durar más de diez días. Para acortar el tiempo, se puede utilizar la Fórmula 3, junto con la circulación del electrolito, técnicas ultrasónicas y otros métodos de galvanoplastia de alta velocidad.
5.2.4 Galvanoplastia de alta velocidad.
5.2.4 Vertido del núcleo: Se coloca un núcleo de acero preprocesado en el centro de la cavidad del cátodo (con una tolerancia de concentricidad inferior a 0,5 mm). El espacio entre el molde del cátodo y el núcleo de acero se rellena con aleación fundida de bajo punto de fusión o resina epoxi mezclada con agentes de curado y rellenos.
5.2.5 Vertido del núcleo: El núcleo de acero se coloca en el centro de la cavidad del cátodo.
5.2.5 Mecanizado: El agujero interior y las caras de los extremos del núcleo de acero se mecanizan con el molde del cátodo como referencia. El orificio interior se procesa con la precisión requerida en una rectificadora interna de alta precisión con una rugosidad superficial de Ra0,1, y la cara extrema se rectifica en una rectificadora externa para garantizar la perpendicularidad con el orificio.
5.2.6 Mecanizado del núcleo de acero: El núcleo de acero y las caras extremas se mecanizan con el molde catódico como referencia.
5.2.6 Retirada de la carcasa: El molde del cátodo se apaga tomando como referencia el taladro interior, dejando un margen de 0,5 mm. El molde restante se retira con una herramienta de torno de conformación y se recorta el perfil del rodillo. Por último, se utiliza una muela de perfil en una rectificadora específica para terminar el perfil del rodillo. Tras una inspección de precisión y los ajustes necesarios, se completa el producto acabado.