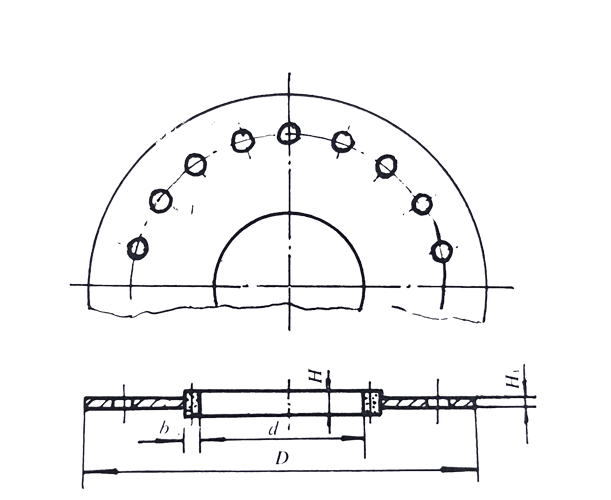
Table of Contents
1.電着研磨ヘッド
研磨ヘッドの形状は、円筒形と様々な特殊形状(台形、楕円形、四角形、円錐形、炎形など)があります。直径サイズは0.2mmから15.7mmまで。芯棒は旋盤で加工されます。半径方向の振れは、関連要件に厳密に準拠する必要があります。
図1 電解研磨棒の直径は0.2 mmから15.7 mmまでです。
図1 電気メッキ研磨ヘッド
1.
1.1 プロセスの流れ
心棒加工→心棒検査→機械的均し→化学的脱脂(30~60分)→湯すすぎ→冷水すすぎ→冷水すすぎ→絶縁塗料塗布→ワイヤー溶接→治具取り付け→電解脱脂→冷水すすぎ→冷水すすぎ→濃塩酸エッチング(1分)→冷水すすぎ→希硫酸による化学的または電気化学的活性化(0.5~1分)→空めっき槽への直接通電(10分)→砂埋め法→厚付け(陰極移動)→冷水すすぎ→洗浄→脱脂・除錆→湯すすぎ→冷水すすぎ→光沢層の電気めっき(Ni、NiCo合金、Cu-Ni-Cr)→冷水すすぎ→水素除去→品質検査。
1.2 プロセスのポイント
1.2.1 砂投入冶具 砂投入冶具は、多孔質有機ガラス製の直線状の砂溝をナイロンクロスで裏打ちした溝型冶具を使用する。複数の研磨ヘッドを砂溝に並べて挿入する。最適な作業方法は、作業端を上向きにして砂をかけることです。
図2フレームは、砂の溝に複数の研磨ヘッドを並べて挿入する。
図2 枠型サンドアプリケーション固定具
フレーム型固定具は、φ3mmの銅線を曲げて四角いフレームを作り、プラスチックの支持板の上に置いたものです。砂をかけるとき、研磨ヘッドは平らに置かれ、銅フレームにはんだ付けされる(図2参照)。片面に砂をかけた後、180度回転させて裏面に砂をかける。1.2.2 砥粒サイズと研磨ヘッド径のマッチング 研磨ヘッド径と適切な砥粒サイズのマッチングについては表1を参照。
1.2.3 砥粒径と研磨ヘッド径のマッチング
1.2.3 シックニング
固定具から取り外された研磨ヘッドは、メッキ槽に吊り下げられ、厚みが粒径の約80%になるまで(つまり80%埋没するまで)増肉されます。その他のポイントを表2に示す。
表2 超硬材料製品の電気メッキプロセスの要点
1.2.4 光輝層めっき
1.2.4 光輝層めっき
1.2.4 光輝層めっき
厚付け工程の後、絶縁材料を除去する。脱脂と除錆の後、研磨ヘッドとその連結棒は保護装飾層で電気めっきされます1.2.4光沢層めっき
研磨ヘッドとその連結棒は保護装飾層で電気めっきされます。
電気メッキされたヤスリの詰め合わせ
電気メッキされたヤスリの詰め合わせ
電気メッキされたヤスリは、手動式と機械式の両方があり、100種類以上の仕様があります。国内では、アソートファイルの典型的なセットには、10~12種類の形状が含まれています(表3参照)。砥粒の粒度は、加工表面の仕上がりに対するユーザーの要求によって決定され、一般に100/120から270/325の範囲である
。表3
2.1 プロセスの流れ
水洗→電線接続→絶縁処理→治具取り付け→電気化学的脱脂→ホットブランク金属加工と成形→表面機械処理→アルカリ化学的脱脂→湯洗→冷水洗→冷水洗→エッチング→前めっき→砂処理→厚付け→冷水洗→洗浄とトリミング→脱脂と脱錆洗浄→光沢めっき→冷水洗→乾燥→検査→商標印刷→包装→保管
。2.2 主な工程のポイント
2.2.1 絶縁クランプ
2.2.1 絶縁クランプ
2.2.1 絶縁クランプ
ファイルブランクはワイヤーに接続され、非作業面はプラスチックフィルムまたはチューブで絶縁される。その後、特別な固定具に取り付けられます。2.2.2 エッチング
2.2.2 エッチング
まず、150~300g/Lの塩酸水溶液で1~2分間エッチングし、その後洗浄し、3~5%の希硫酸水溶液で弱化学エッチングするか、1~3%の希硫酸水溶液で5~10A/dm²の電流で数秒~半分間弱電気化学エッチングします。2.2.3 前めっき
2.2.3 前めっき
2.2.3 前めっき
エッチング後、ファイルを直接帯電させ、電流(ik)を約1A/dm²にして、10~20分間前メッキを行います。2.2.4 サンドアプリケーション
サンドアプリケーションの場合
落砂法では、研磨剤と電解液を入れた有機ガラス鋳型の空洞に、ファイルブランクを入れます。鋳型は、ダイヤモンドを懸濁させるために振られ、その後、砂メッキのために安定化されます。様々な角度から砂を塗布するには、複数回の回転が必要である(表27参照)。砂の塗布電流は1.2 A/dm²を超えないようにし、各砂の塗布時間は、砥粒の大きさが100、120、150の場合、それぞれ8.7分と5分である。砂を埋め込む方法では、ヤスリのブランクを特殊な固定具(図3の枠型固定具)の上に置き、ブランクとその周囲にダイヤモンドを均一にまぶします。砂を1回かける(砂の補充)。砂を埋め込むための電流を流した後、固定具を180度回転させ、0.2~0.5A/dm²の電流を流す。
2.2.5 シックニング
2.2.5 シックニング
2.2.5 シックニング
シックニングの際には、刃先が過度にメッキされたり焦げたりしないように注意しなければならない。遮蔽対策として、保護陰極または絶縁板を使用すべきである。手動アソートヤスリの場合、電着層の厚さは通常、平均粒径の60%~70%に達します。電着ダイヤモンド内面円形切断ディスク ステンレス製の薄ディスク内径のエッジに微細なダイヤモンド層を電着させた、有価物切断用の切断工具です。形状は図3の通り。一般的な粒径は270/325、325/400、またはマイクロパウダー36-54である。典型的な仕様(mm)は、内径d83-130、外径D206-300、H0.2-0.3、H1 0.1-0.2、b0.5-2.03などである。図3 内径切断刃
3.1 プロセスの流れ
3.1 プロセスの流れ: ベースの化学的脱脂 → ディスクの装填 → 電解研磨 → 洗浄 → メッキ浴での逆電流処理 → ベース層のメッキ → ダイヤモンド層のメッキ (砥粒の埋め込みと厚膜化) → 分解と洗浄 → 乾燥 → マーキング → 保管
3.2 工程のポイント:3.2.1 ディスクの装填:数枚の薄いディスク基板と有機ガラス板を、ナイロン布をライナーとして専用の有機ガラス型に交互に入れ、エンドキャップで密閉する。ネジを締めることで、適切な密閉性と導電性が確保される。図4はディスク・アセンブリの概略図である。
図4はディスク組立の概略図である。
図4 内径切断ブレード固定具の概略図
内径切断ブレード固定具の概略図
3.2.2 電解研磨: 電解研磨は、電気化学的溶解によってステンレス鋼表面の緻密な酸化膜を除去し、刃先を薄くする。研磨工程では、50%硫酸水溶液を使用し、1枚あたり2.5~3Aの電流を1~2分間流す。研磨後、内部キャビティは洗浄される。
3.2.3 逆電流処理とニッケルめっき下地:金型キャビティをニッケルめっき液(NaCl 2200g/L、HCl 125g/L)で満たします。基板に1~3分間逆電流処理を行い、その後電流を切り替え、3~5分間ニッケル下地めっきを行う。各ディスクの順電流と逆電流は0.13~0.2Aである。
3.2.4 砥粒の埋め込みと厚付け:金型キャビティをニッケルコバルト合金めっき液(表4参照)で置換し、砥粒とニッケル陽極を装填し、ディスク1枚あたり0.13~0.2Aの電流で砥粒埋め込みと厚付けを行う。砥粒の埋め込みと厚付けの工程は次の通りである:金型を移動し、端面に水平に置き、5分間めっきし、これを2回繰り返す。その後、金型を垂直に置き、60度回転させながら一度に3分間、毎回異なる開始点で4面を覆う工程を繰り返す。最後に、ディスクを平らに置き、表と裏をそれぞれ15分間めっきする(ディスク1枚あたり電流50A)。
表4 めっき液の処方とプロセス条件(濃度はg/L)
4.
4.電気メッキダイヤモンドコアドリル
4.1 コアドリル:コアドリルの形状を図5に示す。仕様は顧客の要求に応じて決定され、一般にD20-100mm、D-D1mm、h5-20mmである。一般的なグリットサイズは50/60、60/70、70/80である。
図5 電気メッキコアドリル
4.1 プロセスの流れ: 装着→ダミーめっき→砥粒埋め込み→厚付け→砥粒埋め込みと厚付けの繰り返し→コアシャフトの取り外し→トリミングと初期検査→全体仕上げ(光沢ニッケルめっき)→ベースとコアシャフトの準備→めっき前の表面処理(化学的脱脂と電気化学的活性化検査)
4.2 重要な工程のポイント
4.2.1 仮のコアシャフト:有機ガラス製コアシャフト(銅またはニッケルで化学メッキ)、低融点合金ロッド、または下地処理されたコア形状の3種類が使用できる。コアシャフトの外径はコアドリルの内径である。これらのコアシャフトは、溶解、加熱して溶かす、旋盤で回すなどの方法で取り除くことができる。
4.2.2 作業層めっき:主な特徴は、仮のコアシャフトをベースとして使用する加工層の放射状電着であり、これによりめっき時間が大幅に短縮される。活性化後、基板はめっき浴に入る。砥粒の埋め込みは埋め込み砥粒方式で行われる(固定具は図6参照)。電解液は式7を使用し、電流は0.2~0.25 A/dm²。砥粒除去後、0.5~1.0 A/dm²の電流で増粘を行う。砥粒の埋め込みと厚付けプロセスは、要求仕様を満たすまで繰り返される(多層グリットめっき)
。図6のコア砥粒は、0.5~1.0 A/dm²の砥粒を埋め込み、必要な仕様(多層砥粒めっき)を満たすまで、砥粒の埋め込みと厚膜化を繰り返します。
図6 コアドリル砥粒埋め込み装置
5.電着ダイヤモンドドレッシングローラー 電着ローラーは、高精度、高効率の先進的なツールです。成形砥石の複雑なプロファイルをドレスするため、またはプロファイル研削のために直接使用されます。ローラーには様々な形状があります。図7に2つの例を示します。砥粒のサイズは加工要件によって異なり、30/35からマイクロパウダーサイズまであります。
図 7 ダイヤモンド・ドレッシング・ローラーの概略図
ダイヤモンド・ドレッシング・ローラーの概略図
単純なローラーは、粉末冶金法または外部メッキ法で製造でき、精度は一般に約0.02 mmです。より複雑で高精度なローラーの電気メッキ工程は、先に述べた製品と同様ですが、砥粒の均一性を確保できるのは内部メッキ法のみです。以下、内部めっき法について紹介する。5.1 内面めっき法の工程フロー:陰極金型の準備→めっき前の表面処理→砥粒の埋め込み→厚付け→電鋳→中子の注入→機械加工→シェル除去→精密トリミングと検査
5.2 内面めっき法の主な工程
5.2 内部めっき法の主な工程ポイント
5.2.1 陰極金型:陰極金型はローラープロファイルに対応する逆金型であり、電気めっきの仮基板として使用される。金型表面の精度は厳密に管理されなければならず、一般にローラープロファイルの精度(1~2 µm)よりわずかに高い。陰極金型は、めっき前に徹底した表面処理を施さなければならない。
5.2.2 砥粒の埋め込み:高精度ローラーでは、特殊な治具を用いたグリット埋め込み方式が採用されている(埋め込み装置は図8、完成構造は図9参照)。電流密度は0.2~0.25A/dm²である。1回目のグリット埋め込み後、金型と固定具を180度回転させて2回目の埋め込みを行う(補助グリット)
。図8 砥粒の埋め込み装置
図9 完成した構造
図9.
5.2.3 増粘と電鋳:フォーミュラ6の電解液を使用し、電流密度は0.5~1A/dm²です。この工程は、ダイヤモンド粒子がめっき層に完全に埋め込まれるまで続けられ、その後、電流を1.5A/dm²以上に上げて電鋳を行い、厚さを2~5mmにします。この工程には10日以上かかることもある。時間を短縮するために、電解液循環、超音波技術、その他の高速電気めっき法とともに、式3を使用することができる
。5.2.4 中子の注湯:前処理された中子をカソードキャビティの中心に配置する(同心度公差は0.5mm以下)。カソードモールドとスチールコアの間の隙間は、硬化剤と充填剤を混ぜた溶融低融点合金またはエポキシ樹脂で満たされる。
5.2.5 機械加工:
5.2.5機械加工:スチールコアの内径と端面は、カソードモールドを基準として機械加工されます。内径は表面粗さRa0.1の高精度内面研削盤で必要な精度に加工され、端面は外面研削盤で内径と直角になるように研削される。
5.2.6 シェルの取り外し:
5.2.6シェル除去:内径を基準として、0.5mmのマージンを残して陰極モールドを外します。残りの金型は成形旋盤工具で取り除かれ、ローラープロファイルが切り取られます。最後に専用研削盤でプロファイル砥石を使用し、ローラープロファイルを仕上げる。精密検査と必要な調整を経て、完成品となる。