チタン合金、ステンレス鋼、耐熱合金、表面硬化金属などの難削材を鋸で切断する場合、超硬チップソーはその優れた切断効率と耐久性により、広く使用される工具となっています。近年では、従来のバイメタル製バンドソーブレードに比べ、切断速度が速く、仕上げ面が滑らかで、寿命が最大20%長いことから、汎用材料にも適用するユーザーが増加している。
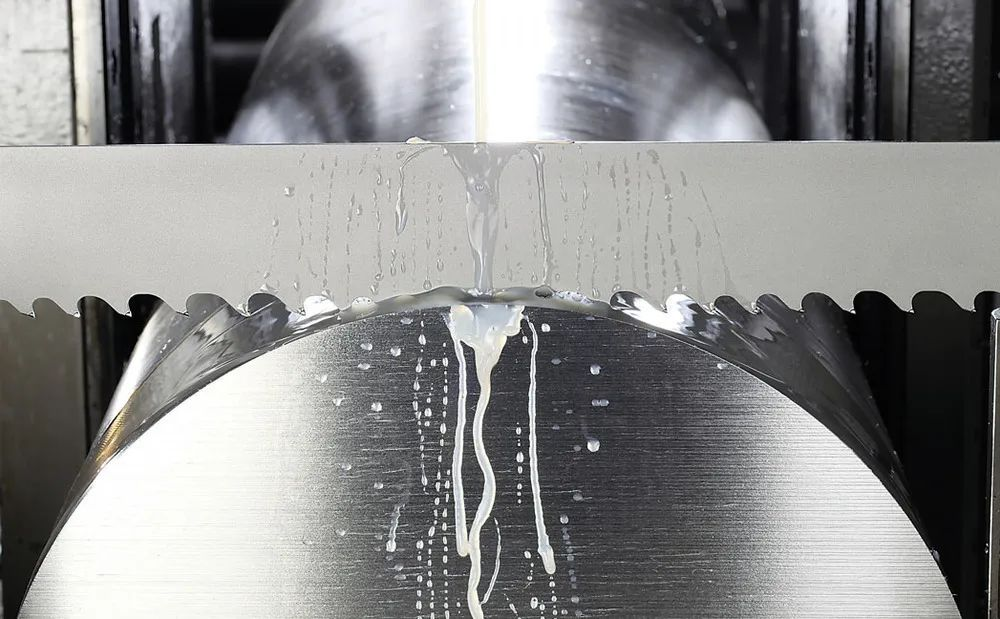
1.歯の構造と形状
超硬チップソーの一般的な歯形には、トリプルチップ切削歯と台形研削歯があります。トリプルチップの歯形は通常、正のすくい角が特徴で、高強度または高硬度の材料に素早く食い込み、効率的に切り屑を形成できるため、生産性の高い加工に最適です。表面硬化材(シリンダーロッドや油圧シャフトなど)には、負のすくい角の歯形が推奨されます。この形状は、高熱条件下で硬い外層を「押しのける」のに役立ち、スムーズな切削を可能にします。
アルミ鋳物のような研磨材には、歯ピッチが広く、チップ溝が大きいバンドソーブレードが適しています。これは、ブレードの後刃にかかるクランプ力を効果的に低減し、工具寿命を延ばすことができるからです。
2.帯鋸刃の種類と用途
小径材 (<152 mm): トリプルチップとポジティブすくい角プロファイルの超硬ブレードに適しており、優れた切断効率と材料適応性を提供します。
大径材料: 各歯先が最大5つの切れ刃で研削され、溶け込みと材料除去率を向上させる多面歯ブレードを推奨。
表面硬化部品: 負のすくい角を持つトリプルチップブレードを使 用することで、硬化した外層を貫通するための高温切 断と迅速な切りくず排出が可能になる。
非鉄金属およびアルミ鋳物: 切り屑が詰まるのを防ぎ、早期破損を 減らすため、歯ピッチの広いブレードを推奨。
汎用切断: さまざまな材料形状と切断需要に対応するため、中立またはわずかに正のすくい角を持つ万能超硬バンドソーブレードを推奨。
3.歯形が切削品質に及ぼす影響
異なる歯形形状は、異なる切りくず形成メカニズムに対応する。例えば、4つの研削歯を使用する設計では、1サイクルに7つの切り屑を生成することができ、各歯が均等に負荷を分担するため、より滑らかで直線的な切削が可能になります。別の設計では、3つの歯を使用して5つの切り屑を形成し、わずかに粗い表面仕上げにもかかわらず高い切削速度を提供し、速度優先の加工に最適です。
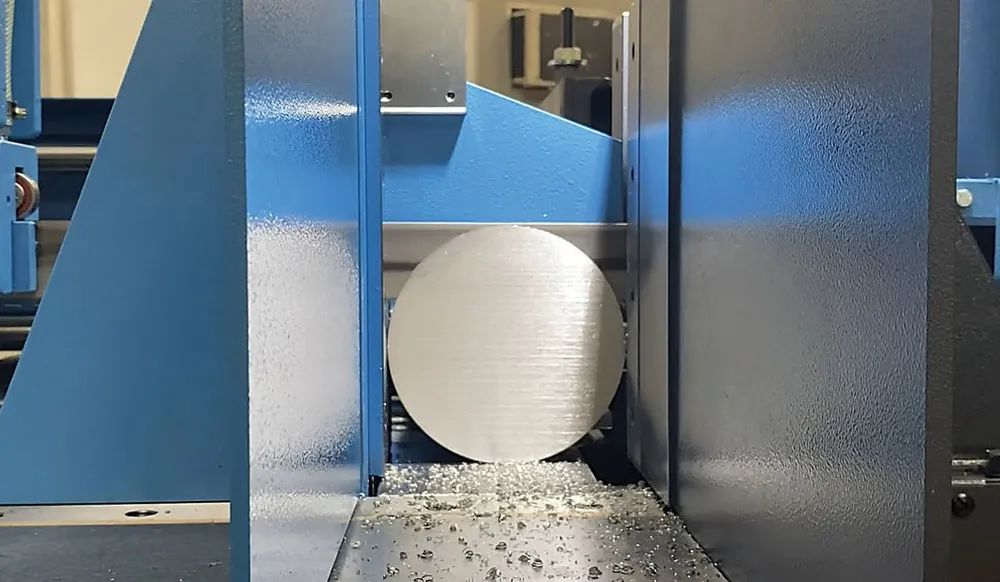
4.コーティングと冷却
窒化チタン(TiN)や窒化アルミニウムチタン(AlTiN)など、耐摩耗性と熱安定性を高めるコーティングを施した超硬チップブレードもあり、高速加工や高送り加工に適しています。ただし、コーティングの選択は実際の作業条件に基づいて行わなければならない。
冷却に関しては、高温合金や高硬度鋼の切削では、熱放散を改善するために、やはり浸水冷却を推奨する。アルミなどの非鉄金属では、潤滑と冷却に乳化油と空気を混合したミスト冷却を採用するのが一般的だ。また、負のすくい角のブレードで高温切削を行う場合、過剰なクーラントが熱衝撃を引き起こし、チップを損傷させることがある。このような場合、刃の側面への低頻度のクーラント滴下は、冷却ではなく潤滑のみに使用することを推奨する。
5.再研磨と工具寿命
非鉄金属に使用される丸鋸やシンカーフソーのような一部の超硬チップ刃は、3~5回の再研磨が可能です。再研磨の回数は、超硬チップのサイズと歯の形状によって制限されます。シンカーフ・ブレードや1回限りのバンドソー・ブレード(鉄金属の切断に一般的)の場合、一般的に再研磨は行わず、故障時に廃棄される。
6.システムの互換性
超硬チップソーブレードの性能は、歯の形状と材質だけでなく、工作機械の状態、冷却システム、オペレーターの経験、材料の特性にも左右されます。ブレードの選択は、加工システム全体の安定性と一貫性を考慮する必要があります。高レベルの機械メンテナンスと工程管理が、超硬チップソーの性能を最大限に引き出す鍵です。