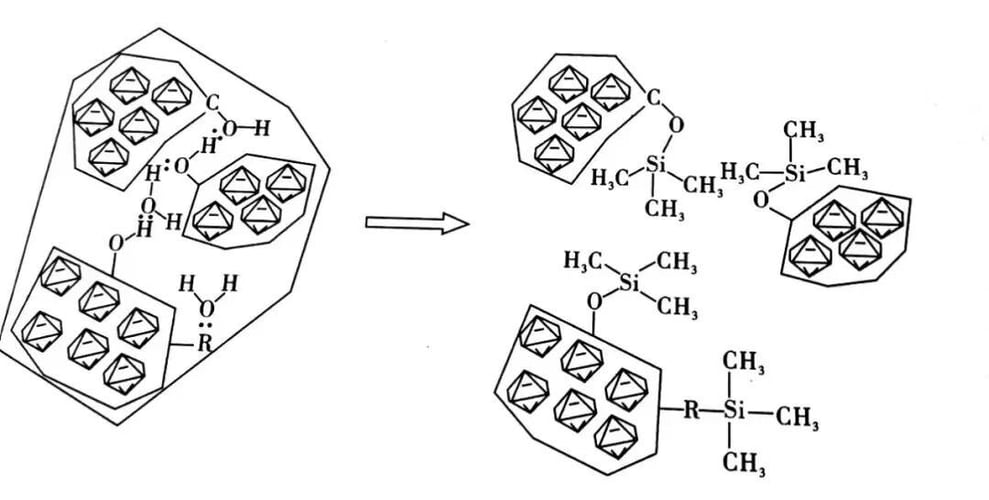
Table of Contents
Surface modification of solid particles refers to the technique of using certain methods to treat, finely modify, and process the surface of inorganic or organic solid particles. This technique aims to purposefully alter the physical and chemical properties of solid particle surfaces to meet the processing and application requirements of solid particles.
Currently, research on surface modification mainly focuses on the following areas:
(1) The study of surface characteristics of inorganic powders;
(2) The mechanism of interaction between inorganic powders and surface modification, and the development of new surface modifiers;
(3) Research on the evaluation methods of modified inorganic powders;
(4) Research on the application of inorganic powders;
(5) Research on the preparation of modified inorganic powders.
In the preparation of nanomaterials, ultrasonic waves can effectively promote the formation of new solid phases, control the size and distribution of particles, resulting in products with small and uniformly distributed particle sizes. During the crystal nucleation phase, ultrasound primarily prevents agglomeration. Additionally, ultrasound can break apart agglomerates and prevent the re-agglomeration of particles. Ultrasonic dispersion technology is commonly used in chemical production, and it is also an effective method for reducing nanoparticle agglomeration. Studies have shown that adopting a reasonable ultrasonic dispersion process can reduce the average particle size of nano-diamonds by more than half.
- Model of Methylsilyl Surface Modification of Nano-Diamonds
In most cases, the surface properties of nano-diamonds depend on their purification method. Since there are significant differences in the surface properties of nano-diamonds produced by different companies, this is related to the lack of a unified purification process. The experiment used nano-diamonds produced by "3AO Diamond Center" (purified by nitric acid). For comparison, nano-diamonds produced by "Arlit" (smoking-nitric acid purification) were also used.
Deionized water from secondary distillation was used as the dispersing agent medium. The surface modification of nano-diamonds involved the solid-phase grafting of methylsilyl groups through a silylation reaction. The molar ratio of Me3SiCl + (Me3Si)2NH (Me for methyl) was 1:1. The reaction ensured the silylation process in the presence of water, where hydroxyl groups underwent silylation. The reaction proceeds as follows:
Me3SiCl + (Me3Si)2NH + 3H2O → 3RO-SiMe3 + NH4Cl
To ensure its effectiveness, the quantity of methylsilyl components needs to be doubled compared to the calculated amount. The methylsilyl mixture was added to a flask, and nano-diamond powder was gradually introduced for mixing. The suspension was then heated to boiling for about 5 hours and left to cool overnight. The remaining methylsilyl mixture was distilled off, and the solid residue was heated under vacuum at 300°C for about 5 hours.
To purify the surface of the nano-diamonds, they were preheated at 430°C under high vacuum (1.33x10^-4 Pa) for 4 hours. The kinetic curve of the adsorption layer reflects the characteristics of the nano-diamond. The total ion flow curve of nano-diamond A exhibits two desorption peaks at 110°C and 280°C. Nano-diamond B does not show obvious peaks; however, the decomposition of the adsorption layer was essentially completed at 360°C.
After vacuum treatment, the size distribution of nano-diamonds dispersed in water fell within the nanometer scale, with 90% of the particles measuring between 18 and 32 nm. After 15 minutes of stabilizing the suspension, the largest particles precipitated out. To maintain optimal dispersion, the nano-diamonds were placed in an ultrasonic field. Experiments showed that the stability of the dispersion was related to the time spent in the ultrasonic field. After the first 5 minutes of treatment, the dispersion curve shifted towards larger sizes (curve 2). After another 5 minutes, the dispersion curve returned to its original form, though some agglomeration occurred. This phenomenon was observed for up to 30 minutes of ultrasonic treatment, with more severe agglomeration occurring with longer durations. For the dispersion of nano-diamonds, the reverse effect of ultrasound may involve a complex process related to the formation and destruction of cavitation bubbles in the ultrasonic field. The most likely explanation is that a surface physicochemical process was triggered. Changes in the surface activity of detonation-synthesized nano-diamonds or changes in the structure of the suspension could be responsible. The initial decrease in particle size was due to the removal of the fusion layer, which promoted agglomeration. When the nano-diamonds were further treated in the ultrasonic field, newly formed agglomerates were dispersed. When placed in ultrasound for more than 20 minutes, the dispersion stabilized for about 3 hours before re-agglomeration occurred. Therefore, to ensure long-term optimal dispersion, the suspension should be periodically placed in ultrasound rather than continuously exposed. It should be noted that in each cycle, some agglomerated nano-diamond particles will precipitate out of the suspension.
Due to the reverse effect of ultrasonic treatment on the dispersion of nano-diamonds in aqueous suspensions, the dispersion of nano-diamonds in aqueous media is dependent on the duration of ultrasonic treatment and may undergo periodic changes.
The study of the structure of nano-diamond suspensions shows that pre-treatment is actually an essential stage for studying the suspension. According to the dispersion of nano-diamond A, about 90% of the particles range from 18 to 32 nm, making them classified as a nanodispersed material.
In non-polar media, the surface modification of nano-diamonds is necessary for dispersion. An effective method for changing surface functional groups is surface silylation, using substances containing -OH, -COOH, -NH2, -SH groups, as well as aldehydes and ketones. It can be speculated that the long-term treatment of nano-diamond A at the boiling point of the reagent ensures the removal of adsorbed water and the covered functional groups, forming methylsilyl functional groups. The organic surface characteristics are related to the grafted trimethylsilyl functional groups, making the surface hydrophobic. The degree of hydrophobicity may be related to the controlled amount of methylsilyl mixture and the chemical properties of the selected organosilicon compound.
Figure 1: Dispersion Model of Silane Coupling Agent for Diamond Modification
Including a functional group with a reactive proton (such as -OH, -NH₂, -COH, etc.)
Assuming that the fractal aggregates are spherical, the effective radius can be expressed as
R=r0N1/dfR = r_0 N^{1/d_f}R=r0N1/df
where NNN is the number of primary particles in the fractal aggregate, dfd_fdf is the effective dimensionality of the fractal aggregate particles, and r0r_0r0 is the effective cluster radius. This dispersion aggregate is formed through hydrogen bonds established by zeolite-type water molecules. The reaction of methyl silane leads to the breakage of these stable hydrogen bonds, resulting in a parameterized dispersion. From the perspective of nanodiamond fractals, they can break into NNN primary-sized nanodiamond particles.
After comprehensive studies on the gas desorption and volatile substances on the surfaces of nanodiamonds of different qualities, it is concluded that to purify the surface of nanodiamonds, in practical applications, a treatment for 4 hours at a desorption temperature of 35°C under a pressure of approximately 10−410^{-4}10−4 Pa is required. During ultrasonic treatment, it is possible to obtain a stable suspension of diamonds sized 18-32 nm in a water medium. The modification of nanodiamonds with methyl silane reagents leads to essential changes in their properties. In a non-aqueous medium, stable suspensions of nanodiamonds may also be obtained. Using trimethyl and dimethyl silane groups can achieve a dispersion of nanodiamonds of 14.5-15 nm in toluene, which is superior to that in aqueous media.
- Ultrafine Mechanical-Chemical De-Agglomeration of Hard-Agglomerated Nano-Diamonds
In recent years, using ultrafine mechanical-chemical methods for the ultrafine grinding and surface modification of powders has become an important means of powder ultrafication and functionalization, making it a promising powder processing technology.
The ultrafine grinding equipment used was a high-speed grinding ball mill, with two different grinding aids—D1 and D2. After ball milling, the powder was further chemically and mechanically modified, processed into a suspension, and classified into different particle sizes to meet various application needs.
As ultrafine grinding proceeded, agglomerates were continuously broken down into smaller agglomerates. The surfaces of individual particles exhibited unsaturated bonds and charged structures, leaving the particles in a metastable, high-energy state.
The two suspensions, based on the different surface properties of nano-diamonds, can be used for different applications. D1 grinding-aided suspension had a simple diamond surface and was used for composite plating applications without contamination, making it suitable for composite plating. The D2 grinding-aided suspension exhibited good stability and uniformity in both strong acidic and alkaline ranges, making it more suitable for ultra-precision polishing applications.
Table 1 provides the particle size distribution and activation index of the suspension after ball milling with two different grinding aids. Compared to no grinding aids, the addition of the two grinding aids resulted in a significant grinding effect, with finer particle sizes and much higher activation indices. Of the two, D2 grinding aid performed better, with a final suspension particle size distribution within 100 nm, an average particle size of 45 nm, and an activation index of 87.8%.
- De-Agglomeration and Dispersion of Nano-Diamond Agglomerates in White Oil
Research on the de-agglomeration and dispersion of nano-diamonds in white oil shows that mechanical-chemical treatment can modify the surface of nano-diamonds. Utilizing the synergistic effects of mechanical force and chemical activators can effectively crush nano-diamond agglomerates while modifying the newly formed surfaces, regulating the hydrophilic and hydrophobic properties of the particles, and increasing the repulsive forces between particles. This results in the stable dispersion of nano-diamonds in white oil.
The experimental samples were detonation-synthesized and purified nano-diamond gray powder, with a purity of over 95%, a primary particle size of all particles below 60 nm, an average particle size of 12 nm, and a cumulative distribution median particle size of 8.5 nm. However, due to the high surface energy, nano-diamonds existed in the form of severe agglomerates. Figure 1 shows that in the white oil system, nano-diamond powder experienced severe agglomeration, clustering, and settling, with agglomeration more severe than in the water medium. Particle size distribution in the white oil system was highly uneven, with only a small portion of particles in the nanometer range. The cumulative distribution median particle size in the system was about 2500 nm.
Xiangyang Xu et al. modified nanodiamonds by adding polymers during the mechanochemical depolymerization process, effectively addressing the issues of depolymerization and dispersion of nanodiamonds in non-polar systems like white oil. They developed a polishing slurry containing nanodiamonds suitable for polishing computer magnetic heads, achieving a surface roughness of less than 0.20 nm while ensuring a high polishing rate.
Figure 2: Particle Size Distribution of Nanodiamonds in White Oil and Water Systems