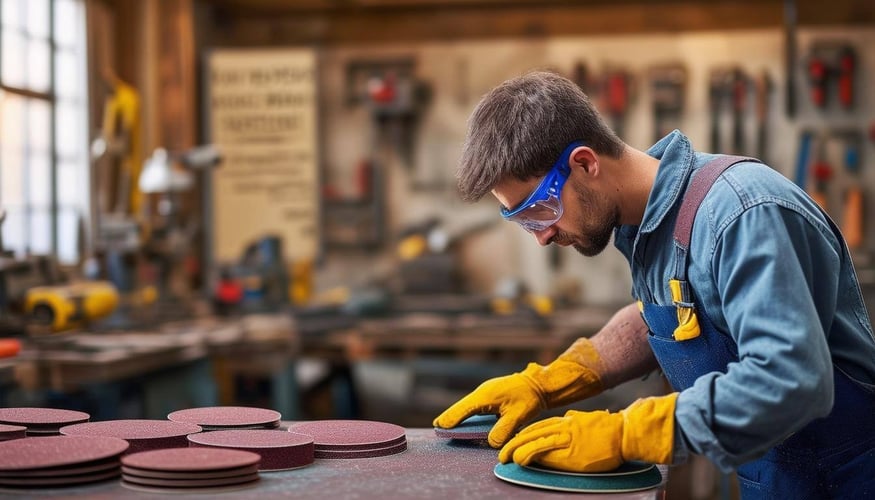
Table of Contents
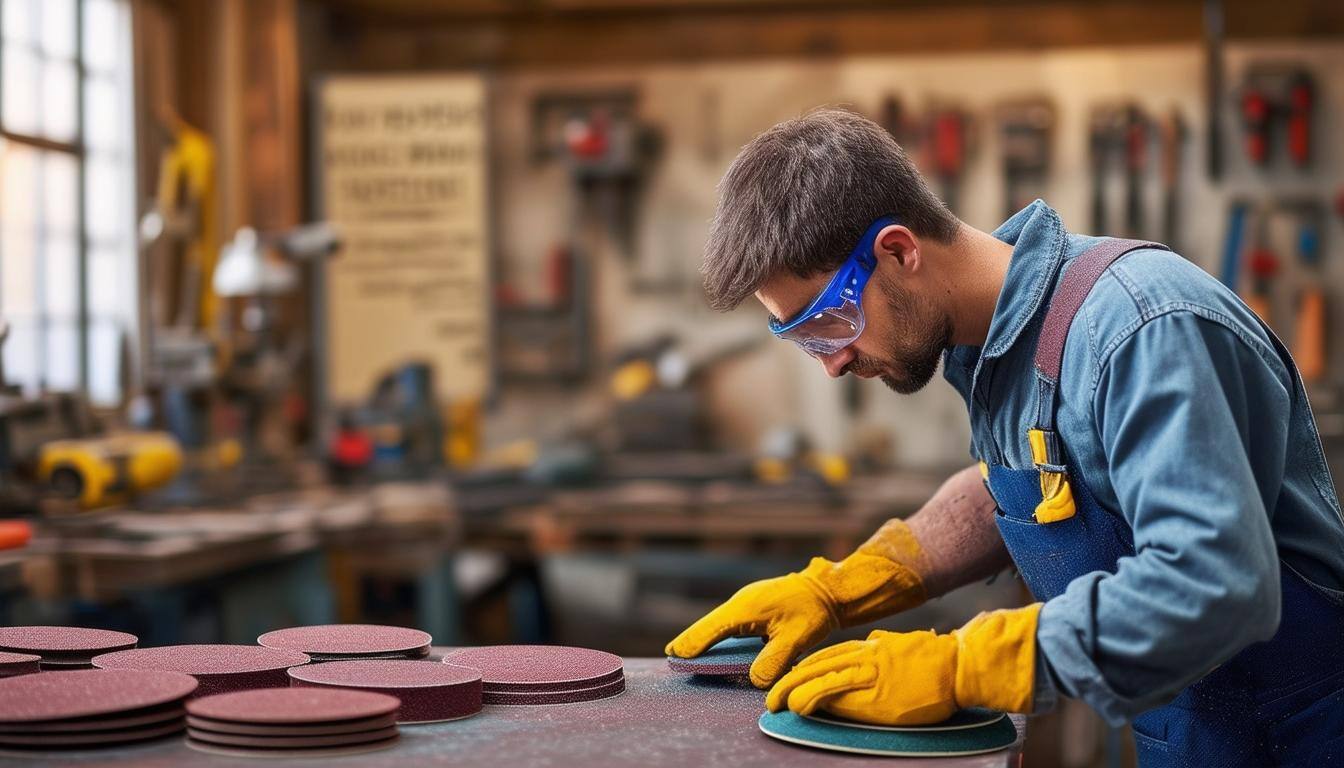
Understanding the Different Types of Abrasives
The Importance of Abrasives in Modern Industries
Abrasives play a pivotal role in modern manufacturing and processing industries. Often referred to as the "industrial teeth," these materials are essential for cutting, grinding, polishing, and finishing processes. The use of abrasives ensures that parts and components meet stringent technical requirements, thus enhancing the quality and durability of the final product. From automotive manufacturing to aerospace engineering, and even in everyday items like kitchen knives and electronic devices, abrasives are integral to achieving precision and efficiency.
In addition to metal processing, abrasives find extensive applications in non-metallic material industries. For instance, in ceramics and glass production, abrasives are used to achieve smooth finishes and intricate designs. In the paper industry, they help in the polishing of surfaces to ensure a fine texture. Thus, the versatility and indispensability of abrasives make them a cornerstone in various sectors.
Corundum Abrasives: Characteristics and Uses
Corundum abrasives are among the most commonly used abrasive materials. Known for their hardness and durability, corundum abrasives are typically composed of aluminum oxide. These abrasives are particularly effective in grinding and cutting applications due to their high resistance to wear and tear.
Corundum abrasives are widely used in metalworking industries for tasks such as deburring, surface finishing, and precision grinding. They are also employed in the production of grinding wheels, sandpapers, and various cutting tools. The ability to maintain their form and sharpness over extended periods makes corundum abrasives a preferred choice for high-precision applications.
Moreover, corundum abrasives are not limited to metal processing. They are also used in the woodworking industry for sanding and finishing tasks. Their versatility extends to the manufacturing of plastics and rubber, where they help in creating smooth and polished surfaces.
Silicon Carbide Abrasives: Features and Applications
Silicon carbide abrasives are another popular choice, known for their exceptional hardness and thermal conductivity. These abrasives are particularly suitable for applications involving high-speed grinding and cutting. Silicon carbide is often used in the production of abrasive papers, grinding wheels, and cutting discs.
One of the standout features of silicon carbide abrasives is their ability to work effectively on both hard and soft materials. They are commonly used in the automotive industry for tasks such as engine component finishing and brake pad manufacturing. Silicon carbide abrasives are also employed in the aerospace sector for precision grinding of turbine blades and other critical components.
In addition to metalworking, silicon carbide abrasives are extensively used in non-metallic material processing. For example, in the glass industry, they help achieve smooth and clear finishes on glass surfaces. Silicon carbide's ability to withstand high temperatures makes it ideal for use in refractory applications as well.
Natural vs. Artificial Abrasives: Pros and Cons
The choice between natural and artificial abrasives depends on various factors, including the specific application and desired outcomes. Natural abrasives, such as emery and garnet, are directly processed from natural ore rocks. They are often preferred for their eco-friendly properties and lower cost. However, natural abrasives may lack the consistency and uniformity required for high-precision tasks.
On the other hand, artificial abrasives, such as synthetic diamonds and cubic boron nitride, are engineered to meet specific performance criteria. These abrasives offer superior hardness, durability, and uniformity, making them ideal for demanding applications. The primary drawback of artificial abrasives is their higher cost compared to natural alternatives.
In summary, the choice between natural and artificial abrasives boils down to the specific requirements of the task at hand. While natural abrasives are suitable for general-purpose applications, artificial abrasives are preferred for high-precision and high-performance tasks.
Common Tools and Products Made from Abrasives
A wide range of tools and products are made from abrasives, each designed to meet specific industrial needs. Common abrasive tools include grinding wheels, cut-off discs, flap wheels, and sanding belts. These tools are essential for tasks such as material removal, surface finishing, and shaping components to meet precise specifications.
Grinding wheels are perhaps the most ubiquitous abrasive tool, used in various industries for sharpening, deburring, and finishing tasks. They come in different shapes and sizes, each tailored for specific applications. Cut-off discs, on the other hand, are primarily used for slicing through metal and other hard materials.
Flap wheels and sanding belts are commonly used for surface finishing and polishing. These tools are essential in industries such as woodworking, metalworking, and automotive manufacturing. The choice of abrasive material in these tools—whether corundum, silicon carbide, or synthetic diamonds—depends on the specific requirements of the task.
The Role of Abrasives in Non-Metallic Material Processing
Abrasives are not limited to metal processing; they also play a crucial role in the processing of non-metallic materials. In the ceramics industry, abrasives are used for shaping, smoothing, and finishing ceramic components. The ability to achieve precise dimensions and smooth surfaces is essential for the quality and functionality of ceramic products.
In the glass industry, abrasives help in cutting, grinding, and polishing glass surfaces to achieve the desired clarity and smoothness. Silicon carbide abrasives are particularly effective in this regard, due to their hardness and thermal stability. Abrasives are also used in the stone and marble industry for cutting and finishing tasks, ensuring that the final product meets aesthetic and functional requirements.
In the woodworking industry, abrasives are essential for sanding and finishing wooden surfaces. They help in achieving smooth textures and intricate designs, enhancing the overall quality of the wooden product. Similarly, in the rubber and plastic industries, abrasives are used for deburring and polishing tasks, ensuring that the components meet precise specifications.
Choosing the Right Abrasive for Your Specific Application
Selecting the right abrasive for a specific application is crucial for achieving optimal results. Several factors should be considered, including the material to be processed, the desired finish, and the specific requirements of the task. For instance, corundum abrasives are ideal for general-purpose grinding and cutting tasks, while silicon carbide abrasives are better suited for high-speed and high-temperature applications.
The choice of bonding agent also plays a significant role in the performance of the abrasive tool. Bonded abrasives, such as grinding wheels, offer high durability and precision, making them suitable for demanding tasks. On the other hand, coated abrasives, like sandpapers and sanding belts, are more flexible and versatile, making them ideal for surface finishing and polishing tasks.
It's also essential to consider the grit size of the abrasive material. Finer grits are typically used for achieving smooth finishes, while coarser grits are suitable for material removal and rough shaping tasks. By carefully selecting the right abrasive material, bonding agent, and grit size, you can ensure that the abrasive tool meets the specific requirements of your application.
Future Trends in Abrasive Technology and Industry Innovations
The field of abrasive technology is continually evolving, driven by advancements in materials science and manufacturing processes. One of the significant trends is the development of superabrasives, such as synthetic diamonds and cubic boron nitride. These materials offer unparalleled hardness and durability, making them ideal for high-precision and high-performance applications.
Another emerging trend is the use of advanced bonding agents, such as ceramic bonds, which offer superior strength and thermal stability compared to traditional bonding agents. These advanced bonds enhance the performance and lifespan of abrasive tools, making them more efficient and cost-effective.
The integration of digital technologies and automation is also transforming the abrasive industry. For example, computer-controlled grinding and polishing systems offer higher precision and consistency compared to manual processes. These automated systems are particularly beneficial in industries such as aerospace and automotive manufacturing, where precision and efficiency are paramount.
In summary, the future of abrasive technology promises exciting innovations and advancements, offering new possibilities for enhancing manufacturing processes and achieving superior results.
By understanding the different types of abrasives and their applications, you can make informed decisions to enhance your manufacturing processes. Whether you're working with metals, ceramics, glass, or other materials, the right abrasive can make a significant difference in the quality and efficiency of your work. Stay informed about the latest trends and innovations in abrasive technology to stay ahead in your industry.