Additive Manufacturing vs. Subtractive Manufacturing: How Abrasive Products Enable Efficient Processing
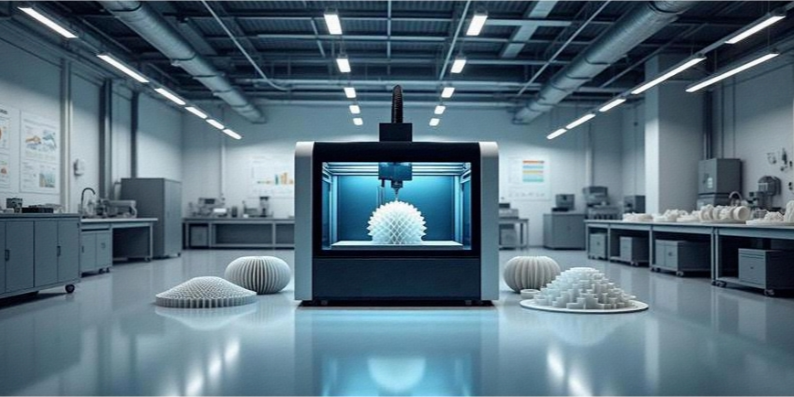
Table of Contents
With continuous advancements in industrial manufacturing technology, precision, efficiency, and design flexibility have become core requirements. Against this backdrop, in addition to traditional subtractive manufacturing (such as milling and grinding), additive manufacturing (3D printing) is gradually gaining traction. Technologies like Selective Laser Sintering (SLS) and Selective Laser Melting (SLM) have been widely applied across various industries.
Both manufacturing methods have their advantages, and combining their strengths can significantly enhance production efficiency and processing quality. In this process, abrasive products play a crucial role—whether in precision post-processing for additive manufacturing or in providing more efficient solutions for subtractive manufacturing. The applications of abrasives continue to expand, driving advancements in precision manufacturing.
Complementary Advantages: The Combined Application of Additive and Subtractive Manufacturing
Since industrialization, advancements in manufacturing technologies have continually optimized production models. Traditional subtractive manufacturing has evolved over the years to achieve high precision, stability, and efficiency in mass production. On the other hand, the emergence of additive manufacturing has addressed limitations in processing complex structures and material utilization, enabling greater design flexibility while reducing raw material waste.
Characteristics and Challenges of Additive Manufacturing
Additive manufacturing, or 3D printing, builds products layer by layer, offering the following advantages:
High Design Freedom: Capable of producing complex geometric shapes and hollow structures.
High Material Utilization: Reduces material waste and improves resource efficiency.
Shortened Development Cycles: Suitable for rapid prototyping and small-batch customized production.
However, additive manufacturing still faces technical challenges such as high surface roughness, limited dimensional accuracy, and structural strength issues, making post-processing essential. Abrasive products play a critical role in this stage. For example, grinding and polishing tools can be used to remove support structures, reduce stair-stepping effects, and improve surface finish, ensuring that 3D-printed parts meet industrial application standards.
Characteristics of Subtractive Manufacturing and the Application of Abrasives
Compared to additive manufacturing, subtractive manufacturing shapes parts by removing material. Common processes include milling, turning, grinding, and laser cutting, with the following key advantages:
High Dimensional Accuracy: Suitable for manufacturing components with strict tolerance requirements.
Excellent Surface Quality: Processed parts exhibit outstanding surface roughness, reducing the need for additional treatments.
Compatibility with Various Materials: Applicable to metals, ceramics, composites, and more.
In subtractive manufacturing, abrasive products are widely used for grinding, polishing, and deburring to enhance precision and surface quality. For instance, high-performance grinding wheels enable precision grinding, improving processing efficiency while extending tool life. Additionally, diamond abrasive products are ideal for ultra-precision machining of high-hardness materials, ensuring component quality.
How Abrasives Enhance Post-Processing in Additive Manufacturing
Additive manufacturing products often require post-processing to meet industrial standards. In this process, abrasives contribute to several key aspects:
Support Structure Removal: Many 3D-printed parts require support structures to maintain printing accuracy. After printing, these supports must be removed. Coated abrasives or soft abrasive tools can efficiently remove support material while preventing surface damage.
Surface Finish Improvement: The layer-by-layer stacking in additive manufacturing can cause a "stair-stepping effect," affecting surface quality. Fine-grit grinding wheels, abrasive discs, or polishing tools can significantly enhance surface smoothness, meeting the high standards of aerospace, medical, and other industries.
Dimensional Accuracy Refinement: Due to the inherent precision limitations of 3D printing, some parts may require additional processing to meet tolerance specifications. High-precision grinding tools, such as diamond grinding wheels, can optimize dimensional accuracy without compromising structural integrity.
Processing and Repair of Special Materials: Traditional machining may struggle with high-temperature alloys, titanium alloys, and other advanced materials. The use of superabrasives, such as CBN or diamond tools, enables more efficient post-processing and repair.
Optimized Applications of Abrasives in Subtractive Manufacturing
In traditional subtractive manufacturing, abrasives play an irreplaceable role in:
High-Efficiency Precision Grinding: High-precision grinding wheels improve dimensional stability and surface quality, reducing the need for additional machining steps.
Extending Tool Life: In metal cutting operations, using high-quality abrasives to condition cutting tools effectively extends their lifespan, lowering production costs.
Deburring and Chamfering: Complex components, such as turbine blades and engine parts, often develop burrs during machining. Abrasive tools efficiently remove burrs and perform chamfering to ensure assembly precision.
Micro-Finishing: In aerospace and medical industries, ultra-precision components require extremely high surface finishes and accuracy. Diamond grinding plates and fine polishing tools meet these stringent demands.
Abrasives Driving Manufacturing Technology Upgrades
Whether in additive or subtractive manufacturing, abrasives play a key role in improving machining precision, enhancing surface quality, and optimizing post-processing efficiency. As the manufacturing industry moves toward higher precision, efficiency, and automation, the applications of abrasive products will continue to expand, providing advanced solutions for aerospace, automotive, medical, and mold manufacturing sectors.
Looking ahead, with the continuous advancement of new abrasive materials, intelligent grinding equipment, and automated processing technologies, abrasives will play an increasingly significant role in the manufacturing industry—driving industrial upgrades, enhancing production efficiency, and improving product quality.