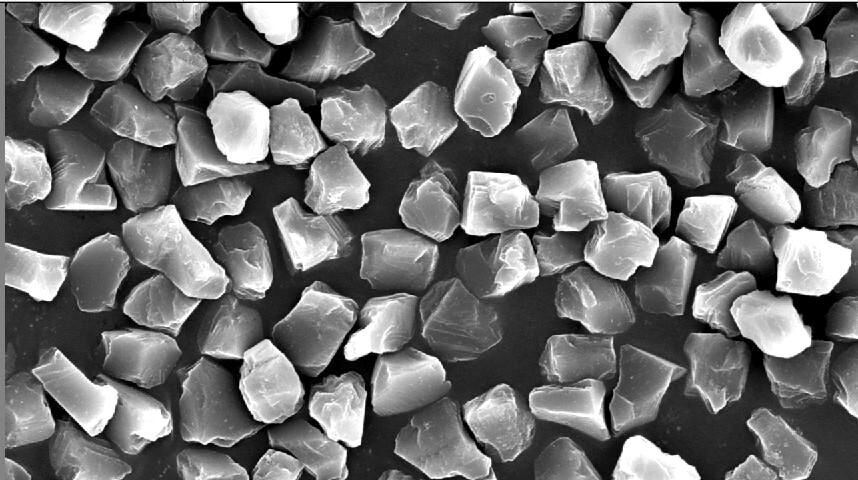
Table of Contents
- El significado significativo y el valor del desarrollo del cBN policristalino .
La aparición del nitruro de boro cúbico (cBN) ha aportado inmensas ventajas al procesamiento de metales y aleaciones endurecidos a base de hierro. Sin embargo, la síntesis de cBN requiere condiciones de presión y temperatura muy elevadas, lo que plantea problemas debido a las limitaciones de los equipos de alta presión y las tecnologías de síntesis. Es muy difícil conseguir cristales de cBN de alta calidad y grano grande. Normalmente, el tamaño de los monocristales de cBN es inferior a 0,5 mm, e incluso los sintetizados mediante el método de gradiente semilla-temperatura tienen tamaños en torno a los 3 mm. Estas dimensiones tan pequeñas sólo son adecuadas para aplicaciones directas en abrasivos y muelas, por lo que son demasiado pequeños para herramientas de corte.
Además, aunque el nitruro de boro cúbico monocristalino es muy duro, su rendimiento en determinadas aplicaciones de procesamiento sigue siendo inferior al ideal debido a los efectos de su estructura de división cristalina. Dada la incapacidad actual para fabricar monocristales de alta dureza lo suficientemente grandes para herramientas de corte, ¿hay alguna forma de abordar mejor este problema?
Esto condujo al desarrollo del cBN policristalino, los cuerpos sinterizados y los materiales compuestos. Estas tecnologías abordan el problema del tamaño del cBN, permitiendo la producción de materiales de cBN a granel con tamaños de partícula que oscilan entre 0,5 mm y 50 mm. Además, como estos materiales tienen una estructura policristalina, no presentan problemas de escisión, lo que mejora notablemente la tenacidad de los materiales de cBN. En consecuencia, la tecnología de cuerpos sinterizados policristalinos y materiales compuestos ha florecido.
¿Qué son los materiales policristalinos y microcristalinos de cBN?
Los materiales policristalinos de cBN están formados por muchos pequeños monocristales de cBN interconectados en un agregado orientado aleatoriamente. Además de tener las propiedades de los materiales monocristalinos, la orientación aleatoria de los cristales individuales dentro del agregado supera la anisotropía de los materiales monocristalinos, proporcionando un rendimiento superior en términos de tenacidad.
El cBN microcristalino se compone de numerosos monocristales de cBN de tamaño submicrónico, con tamaños de partícula que oscilan entre 0,1 y 0,8 mm. En las estructuras microcristalinas, los planos de clivaje están orientados aleatoriamente y forman una estructura bastante densa, que exhibe una gran dureza y resistencia al desgaste frente a la macrofisuración en todas las direcciones.
El nitruro de boro cúbico microcristalino fue introducido por General Electric en la década de 1980 con la marca Borazon CBN550. En comparación con el nitruro de boro cúbico monocristalino, este producto tiene las siguientes características:
Nitruro de boro cúbico microcristalino.
(2) La estabilidad térmica alcanza hasta 1473 K;
(3) Los bordes de corte múltiples permiten una alta eficiencia y precisión de procesamiento;
(4) Autoafilado;
(5) Grano abrasivo de mayor tamaño;
(4) Autoafilado
(6) La estabilidad térmica sigue siendo no inferior a la de los materiales monocristalinos, alcanzando 1200°C;
(7) La forma de múltiples filos aumenta el poder de agarre en el producto, mejorando el filo de corte y la eficiencia;
(8)
(8) El tamaño de los granos microcristalinos puede superar los 0,5 mm, superando las limitaciones de sintetizar cBN de grano grande debido a los equipos de alta presión.
General Electric ha comparado el nitruro de boro cúbico monocristalino y microcristalino, descubriendo que al rectificar aleaciones difíciles de procesar como M-2, M-4 y T-15, la selección de agentes aglutinantes y tamaños de grano adecuados permite que el nitruro de boro cúbico microcristalino alcance eficiencias de rectificado que normalmente duplican las del CBN-ll de Borazon.
Debido a sus características superiores en comparación con los monocristales, el cBN microcristalino ha encontrado amplias aplicaciones en el procesamiento industrial.
Cuando se utilizan muelas de cBN para rectificar aceros con bajo contenido en carbono, aceros aleados blandos y aceros aleados duros resistentes a altas temperaturas, las virutas de metal resultantes tienden a ser más largas, anchas y gruesas en comparación con las producidas con carburo cementado. Para seguir cortando, es necesario limpiar las virutas y rectificar la muela. Además, la presencia de estas virutas metálicas puede erosionar los agentes aglutinantes de la muela, creando picaduras. Si estas picaduras tienen un tamaño comparable al de los granos abrasivos, pueden arrancar granos de la superficie de la muela, acelerando su desgaste. Reducir el tamaño del grano para evitar estos fenómenos disminuiría significativamente la eficacia del rectificado, lo que es económicamente indeseable. La introducción y aplicación de cBN microcristalino puede resolver eficazmente estos problemas. En general, el mayor tamaño de grano, la mayor eficacia de rectificado y la forma irregular del cBN microcristalino mejoran la capacidad de agarre. Cada uno de los cristales de la estructura microcristalina tiene un tamaño de partícula pequeño, lo que evita la formación de virutas largas y fibrosas durante el procesamiento y garantiza que el desgaste se produzca a menor escala dentro de la estructura microcristalina. Esto permite una alta eficiencia de corte y una mayor vida útil de la herramienta al cortar los materiales mencionados, logrando un equilibrio óptimo.
El cBN microcristalino también presenta un excelente rendimiento térmico. A menudo existen tensiones residuales en los abrasivos monocristalinos de cBN, y estas tensiones pueden provocar la fractura del cristal a unos 700°C, lo que repercute en la vida útil del producto. Los experimentos realizados con cBN microcristalino indican que los abrasivos cBN550 conservan su tenacidad incluso tras la exposición a altas temperaturas de 1200°C. Esto no sólo aumenta la vida útil del producto debido a la resistencia al calor del cristal, sino que también permite el uso de agentes adhesivos de alta temperatura en la fabricación, que es otro factor crucial en la ampliación de la longevidad del producto.
La resistencia al calor del cBN microcristalino es una de las características más importantes del cBN550.
- Fabricación de microcristales .
Los microcristales pueden fabricarse por dos vías: la sinterización del nitruro de boro hexagonal (hBN) y del nitruro de boro cúbico (cBN). Un método económicamente viable consiste en la transformación de hBN con la participación de aditivos. El flujo del proceso es el siguiente: mezcla de hBN con aditivos → síntesis → granulación → limpieza → cribado → ensayo.
El hBN utilizado para la fabricación de microcristales requiere un bajo contenido de impurezas, que puede lograrse tratando el hBN a aproximadamente 2273 K para eliminar las impurezas. Además, pueden seleccionarse aditivos de nitruro de boro de alta pureza como Mg₃N₂, Ca₃N₂, Li₃N, o AlN, con una dosificación adecuada que suele oscilar entre el 3% y el 10%; tanto las cantidades excesivas como las insuficientes pueden afectar a la calidad de los granos abrasivos.
Después de mezclar uniformemente el hBN tratado con los aditivos, se produce el ensamblaje, controlando la temperatura de síntesis entre 1773 y 2273 K, la presión entre 5 y 7 GPa, y el tiempo de síntesis entre 5 y 30 minutos. A continuación, los microcristales resultantes se trituran utilizando una trituradora de mandíbulas, con la separación entre las placas de las mandíbulas ajustada según sea necesario para lograr diferentes tamaños de gránulo, seguido de limpieza y cribado.
El uso de PcBN para el corte en seco y a alta velocidad puede reducir los costes de procesamiento. Sin embargo, en comparación con las aleaciones duras tradicionales y las herramientas cerámicas, la preparación y síntesis de las herramientas de PcBN son relativamente desafiantes. Las herramientas de PcBN deben cumplir los dos requisitos siguientes:
(1) Los materiales de las herramientas de PcBN deben estar estandarizados para satisfacer las necesidades de las diversas aplicaciones de procesamiento de materiales.
(2) Al mismo tiempo que se cumplen los requisitos de calidad y consistencia de las piezas de trabajo procesadas, los procesos de producción y síntesis deben simplificarse al máximo para reducir costes.
En esta sección se presentará la influencia en el rendimiento del nitruro de boro cúbico policristalino (PcBN) desde aspectos como la selección del sustrato, la selección del agente adhesivo, la selección del tamaño de grano del CBN y la selección del proceso de síntesis.
3.1 Selección del sustrato
El nitruro de boro cúbico policristalino (PcBN) utiliza una aleación dura como sustrato, sobre la que se coloca una capa de polvo fino de cristal único de cBN mezclado con un agente aglutinante y después se sinteriza a alta temperatura (1400-2600°C) y alta presión (7-9 GPa). La investigación sobre herramientas de PcBN se centra generalmente en cómo mejorar la vida útil de la capa de PcBN y proporcionar una capa intermedia adecuada entre la capa de PcBN y el sustrato, mientras que se presta menos atención al rendimiento del propio sustrato. De hecho, el sustrato tiene un impacto significativo en el rendimiento del PcBN. Por ejemplo, las microfisuras dentro de la capa de PcBN pueden propagarse al sustrato durante el procesamiento; si el sustrato tiene un buen rendimiento, puede evitar la propagación de las fisuras y mejorar así la longevidad de la herramienta.
Los materiales de sustrato comunes son aleaciones duras, que se forman sinterizando una mezcla de partículas de WC, TiC, TaC y agentes aglutinantes (Fe/Co/Ni). Su resistencia al desgaste mejora con la reducción del tamaño de grano y el contenido de cobalto, mientras que la resistencia al impacto aumenta con la ampliación del tamaño de grano y el contenido de cobalto. El sustrato de aleación dura deseado puede obtenerse ajustando el tamaño de grano del WC y el contenido de cobalto. Además de centrarse en las propiedades mecánicas del sustrato, también debe prestarse atención a las propiedades térmicas, como la conductividad térmica y la resistencia a la fatiga térmica.
Los experimentos han demostrado que:
(1) Los materiales de sustrato con tamaños de grano de WC más grandes presentan una mayor resistencia a la fatiga térmica.
(2) La conductividad térmica aumenta con los tamaños de grano más grandes y la reducción del contenido de cobalto.
(3) Los sustratos con granos gruesos y alto contenido en cobalto muestran mejores propiedades antifricción y tenacidad a la fractura.
Por lo tanto, para obtener un material de sustrato con buenas propiedades mecánicas y térmicas, el tamaño de grano del WC debe mantenerse entre 7-9 μm, con un contenido de impurezas controlado por debajo del 0,01%. El contenido de cobalto debe mantenerse entre el 10% y el 16%.
.
3.2 Selección de los agentes de unión
Debido al pequeño tamaño de partícula del cBN monocristalino y a la presencia de planos de escisión fácilmente escindibles, el PcBN policristalino se utiliza predominantemente como herramienta de corte en la industria. El PcBN se compone de numerosos monocristales de cBN pequeños y no direccionales y de agentes aglutinantes. Dependiendo de si se incluye un agente aglutinante en el sistema, puede clasificarse como PcBN con agentes aglutinantes o PcBN puro. Una densa película de óxido de boro en la superficie de los monocristales de cBN obstaculiza la unión directa de los granos de CBN, lo que dificulta la obtención de PcBN puro de alta resistencia. Por lo tanto, es necesario añadir diversos materiales de unión durante el proceso de polimerización para mejorar las conexiones entre los granos de cBN.
Actualmente, existen tres tipos de agentes de unión para el PcBN, tanto a nivel nacional como internacional.
3.2.1 Agentes de unión de metales y aleaciones metálicas
La selección de los agentes de unión metálicos debe cumplir los requisitos de rendimiento para el corte y procesamiento de herramientas de PcBN.
En primer lugar, los elementos del agente aglutinante deben elegirse entre Fe, Co y Ni, y su contenido debe representar entre el 40% y el 50% del agente aglutinante.
En segundo lugar, los elementos del agente aglutinante deben elegirse entre Fe, Co y Ni.
En segundo lugar, los agentes aglutinantes deben seleccionarse entre Cr, Mo, W, La, Ce, Y, Nb, Ta, Zr, V, Hf, Al, Ti, con un contenido del 50% al 60% de la masa del agente aglutinante.
En tercer lugar, los oligoelementos de aleación deben seleccionarse entre C, Mg, S, Si, Cu, P, B, N, Sn. El principio de selección es asegurar una unión firme de los granos de cBN al tiempo que se forman aleaciones ultrarresistentes al calor para garantizar el rendimiento a altas temperaturas de las herramientas de PcBN (siendo las aleaciones de Ti una mejor elección). Además, para garantizar una alta dureza y resistencia al desgaste de las herramientas de PcBN, el contenido de cBN no debe ser inferior al 70%, preferiblemente entre el 75% y el 85%. El tamaño medio de grano del cBN debe ser comparable al del sustrato, alrededor de 9 μm. Además, no se puede añadir más del 5% de óxidos de tierras raras al agente de unión para mejorar la resistencia al desgaste del PcBN.
.
3.2.2 Agentes adhesivos cerámicos
Los agentes de unión cerámicos suelen incluir óxidos y carburos metálicos, boruros, nitruros y óxidos de elementos de los grupos IV, V y VI de la tabla periódica, como Al₂O₃, TiN, TiC, TiCN, AlN, AlB₂, AlCN, etc. Aunque las fases cerámicas son resistentes al calor y tienen una gran dureza, también son considerablemente quebradizas. Se pueden utilizar métodos de endurecimiento para mejorar la resistencia al impacto de las herramientas de PcBN basados principalmente en agentes de unión cerámicos, como el aumento de los bigotes, el endurecimiento por transformación de fase y la adición de trazas de elementos de tierras raras. Entre estos, el endurecimiento por transformación de fase del ZrO₂ y el endurecimiento de los bigotes de Si₃N₄, SiC se consideran métodos eficaces.
De acuerdo con el mecanismo de endurecimiento de los bigotes cerámicos, los bigotes deben seleccionarse con módulos elásticos y coeficientes de expansión térmica inferiores o iguales a los del material del sustrato. Los experimentos han demostrado que los módulos elásticos y los coeficientes de expansión térmica de los whiskers de SiC y los whiskers de Si₃N₄ son relativamente cercanos a los del cBN, lo que los convierte en materiales endurecedores ideales para las herramientas de PcBN.
3.2.3 Agentes de unión mixtos metal-cerámica
El PcBN sintetizado utilizando metal y sus agentes aglutinantes basados en aleaciones presenta una buena tenacidad; sin embargo, en condiciones de alta temperatura y alta presión, el agente aglutinante tiende a reblandecerse, dando lugar a una baja dureza y una escasa resistencia al desgaste. Los agentes aglomerantes cerámicos puros pueden resolver estos problemas, pero la tenacidad y la resistencia al impacto del PcBN sintetizado siguen siendo deficientes, lo que provoca astillamiento y una vida útil corta de la herramienta durante su uso. Los agentes adhesivos mixtos compuestos de cerámica y metales pueden compensar las deficiencias de ambos tipos.
Cuando se sintetiza PcBN con un agente de unión metal-cerámica, se ha descubierto que una fórmula de Al + Ni + Ti(C,N) + Co da como resultado la mejor resistencia al desgaste y tenacidad al impacto. Durante el proceso de sinterización, el Ni y el Co se encuentran en estado fundido, generando nuevas fases que encapsulan el Ti(C,N), mejorando la fuerza de unión del PcBN. El contenido porcentual de Co y Ti(C,N) influye significativamente en el rendimiento del PcBN. Cuando el porcentaje de Co aumenta del 3% al 5%, el índice de desgaste se incrementa en torno a un 19%, la tenacidad al impacto aumenta aproximadamente un 30% y la dureza se incrementa en torno a un 14%. Cuando el porcentaje de Ti(C,N) aumenta del 1,5% al 3%, la relación de desgaste aumenta aproximadamente un 6%, y la resistencia a la flexión aumenta aproximadamente un 12%.
Los estudios de DRX han demostrado que el Co permanece completamente en estado fundido durante la sinterización y reacciona químicamente con el cBN para generar nuevas fases como el Co₀.₄₇N y Co₂B, que encapsulan el Ti(C,N) y crean una fuerte unión interfacial, formando una densa estructura de red que aumenta la densidad del cuerpo sinterizado. Se puede añadir una pequeña cantidad de WC para formar una solución sólida con TiC y TiN, mejorando el rendimiento global del PcBN, pero la cantidad no debe ser excesiva.
3.4 Selección del tamaño de grano de cBN
Las investigaciones indican que un tamaño de partícula mixto de cBN rinde mejor que un tamaño de partícula único, y es preferible un rango más amplio de tamaños de partícula mixtos que un rango estrecho. Esto se debe a que el tamaño de las partículas de cBN afecta directamente a la tenacidad del PcBN: los tamaños de partícula más grandes mejoran la resistencia al desgaste mecánico, pero reducen la resistencia a los daños, lo que da lugar a una menor nitidez de las herramientas de corte producidas. Los tamaños de partícula mixtos pueden mejorar eficazmente el estado de empaquetamiento de los granos; una mayor densidad de empaquetamiento da lugar a una cristalización más completa durante la síntesis.
3.5 Selección del proceso de síntesis
Los métodos de calentamiento pueden incluir calentamiento eléctrico directo o sinterización por plasma de chispa (SPS), también conocido como sinterización por corriente eléctrica pulsada (PECS) y técnica de sinterización asistida por campo (FAST). Se trata de una nueva tecnología de preparación de materiales rápida, a baja temperatura, eficiente desde el punto de vista energético y respetuosa con el medio ambiente. En esta técnica, se hacen pasar pulsos de corriente continua entre las partículas de procesamiento, generando calor Joule dentro de las partículas, lo que provoca diferencias de temperatura de cientos a miles de grados, facilitando la formación, expansión y densificación de los cuellos de sinterización. El consumo de energía es sólo de 1/5 a 1/3 del de los procesos de sinterización tradicionales (como la sinterización sin presión, el prensado en caliente y el prensado isostático en caliente).
La tecnología SPS tiene ventajas incomparables sobre el prensado isostático en caliente:
(1) Sinterización rápida (generalmente, la densificación tarda sólo 0-10 minutos, mientras que el prensado en caliente y el prensado isostático en caliente requieren 120-300 minutos);
(2) Temperaturas de sinterización más bajas (en comparación con el prensado en caliente y el prensado isostático en caliente, las temperaturas de sinterización se pueden reducir en 200-300°C);
(3) Mecanismo de sinterización único (calentamiento interno del polvo con efectos de campo eléctrico y magnético);
(4) Funcionamiento sencillo y cómodo, a diferencia del prensado isostático en caliente, que requiere trabajadores altamente cualificados y tecnología de moldes;
(5) Pequeña huella de equipo, alta automatización, y flujo de proceso corto;
(6) No es necesario el preformado del polvo; es posible la sinterización directa en cuerpos densos, lo que la hace especialmente adecuada para la preparación de polvos especiales como materiales esféricos, amorfos o a nanoescala;
(7)
(7) A través del diseño especial de moldes, se puede lograr fácilmente la sinterización a ultra alta presión y la sinterización de gradiente de temperatura, lo que hace que la tecnología SPS sea muy adecuada para la sinterización de materiales de herramientas de PcBN.
- (8)
- Aplicaciones en campos técnicos .
El PcBN isotrópico (nitruro de boro cúbico policristalino) es un material ideal para herramientas y se utiliza ampliamente en las industrias automovilística, aeroespacial y aeronáutica. El PcBN, fabricado con micropolvo de cBN como estructura y un aglutinante como material de unión, es un material compuesto sinterizado en condiciones de presión y temperatura ultraelevadas. Supera las deficiencias del mecanizado de cBN monocristalino. Liu et al. analizaron los efectos de rectificado de diferentes agentes aglutinantes en las herramientas de PcBN y llegaron a la conclusión de que las herramientas de PcBN con base cerámica son las más adecuadas.
El PcBN es un nuevo tipo de material para herramientas superduro de alto rendimiento que surgió en la década de 1970, abriendo amplias perspectivas de aplicación para las modernas tecnologías de mecanizado, como el corte duro, el corte en seco y el mecanizado ecológico. Se ha convertido en el mejor material de herramienta para el mecanizado de alta velocidad, eficaz y preciso de metales negros. Para las herramientas de PcBN utilizadas en el corte duro de alta velocidad, no sólo se requiere una buena resistencia al calor (estabilidad térmica y resistencia a la oxidación), sino que también es crucial que los materiales de las herramientas de PcBN presenten buenas propiedades mecánicas a alta temperatura, resistencia al choque térmico, larga vida útil de la herramienta y alta seguridad y fiabilidad.
Además del rendimiento del material en sí, el diseño del ángulo geométrico de los materiales de las herramientas de PcBN también es fundamental. El rendimiento de corte de las herramientas de PcBN incluye principalmente la vida útil de la herramienta y la calidad de la superficie mecanizada de la pieza. Los parámetros estructurales razonables y las condiciones óptimas del proceso de corte afectan significativamente a la deformación del metal durante el corte, la fuerza de corte, la temperatura de corte y el desgaste de la herramienta, mejorando la eficiencia de la producción al tiempo que garantiza la calidad del procesamiento y la vida útil de la herramienta, reduciendo así los costes de producción para las empresas.
La empresa alemana Becker Diamond ha presentado una plaquita indexable de PcBN, con un contenido de PcBN del 95%, que puede aumentar la vida útil de la herramienta entre un 30% y un 50% al tornear materiales como metales sinterizados, hierro fundido y aleaciones de titanio. Esta plaquita también puede utilizarse para el mecanizado de materiales especialmente duros y tenaces (como la Stellite 20).
Las herramientas de PCBN se aplican en el corte en seco, utilizando procesos de corte avanzados como el torneado en lugar del rectificado, lo que no sólo ahorra inversión en equipos y mejora la productividad, sino que también aumenta significativamente la flexibilidad en el flujo de trabajo de procesamiento. Además, debido al aumento de los costes laborales y a los requisitos de protección del medio ambiente en el siglo XXI, es muy importante promover el uso de herramientas de PcBN para aprovechar plenamente su potencial. A través de la continua investigación en profundidad sobre el proceso de corte y el mecanismo de las herramientas PcBN, se espera que su importancia crezca aún más.