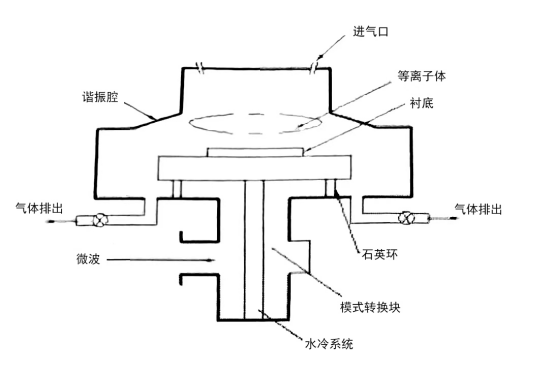
Table of Contents
1980年代にCVDによるダイヤモンド作製法が登場して以来、このダイヤモンド作製法に関する研究は継続的かつ綿密に行われてきた。現代のCVDダイヤモンド作製技術の発展に伴い、さまざまなCVD法が開発されてきました。CVDダイヤモンドの主な作製法には、ホットフィラメント化学気相成長法(HFCVD)、燃焼炎化学気相成長法(CFCVD)、直流プラズマジェット化学気相成長法(DCPCVD)、マイクロ波プラズマ化学気相成長法(MPCVD)などがある。この記事では、これらの蒸着装置の構造と特性について簡単に紹介します。
- 直流アークプラズマ・ジェット法装置
ダイヤモンドの優れた物理化学的特性を十分に活用し、ハイテク分野への応用を促進するため、ダイヤモンド膜の研究が急ピッチで進められている。ホットフィラメントCVD装置は比較的簡単で、大面積のダイヤモンド膜を成長させることができますが、ガスの励起度が低く、ダイヤモンド膜を汚染する可能性があるため、品質要求が低く、コスト重視の工具グレードのダイヤモンド膜の作製に適しています。
図1:直流アークプラズマ・ジェット法装置の模式図
装置は主に、電源システム、水冷システム、真空システム、プラズマトーチなどの構造から構成される。棒状の陰極と円筒状の陽極の間に直流アーク放電が形成され、高温を発生させてAr、H2、CH4などの作動ガスをイオン化する。ガス場と電磁場の影響を受けて、これらのガスは高速で放出され、最終的に基板上にダイヤモンド膜を堆積させる。プラズマの高エネルギーと基板上で起こる一連の反応により、メタン中の炭素原子が結合し、多結晶ダイヤモンドが形成される。他のダイヤモンド膜成膜技術と比較して、直流アークジェットCVD技術には、高プラズマ密度、高イオン化度、高成膜速度(最大900μm/h)、良好なダイヤモンド品質、大成膜面積といった極めてユニークな利点がある。特に、大型の高熱伝導性ダイヤモンド膜ヒートスプレッダーの作製に適しています。
Li Chengming氏らは研究し、直流ジェットプラズマを用いたダイヤモンド合成の現在の方向性は、より大きく高品質なダイヤモンドを製造することに重点を置いていると結論づけている。ダイヤモンドの精密機械加工、宝飾品、光学窓、電子機器などの分野での優れた応用見通しを考慮すると、直流ジェットプラズマはダイヤモンド単結晶の成膜にも使用され、工業化段階に入ろうとしている。ダイヤモンド調製技術のさらなる発展と製造コストの継続的な削減により、その応用範囲と潜在的な市場は急速に拡大するでしょう。CVDダイヤモンド膜の研究は、人工的な産業応用の段階に入り、鉄鋼の時代、単結晶シリコンの時代を経て、人類はより輝かしいダイヤモンドの時代を切り開くだろう:ダイヤモンドと砥粒工学、2018.1:16--27.直流アークプラズマジェット法で作製したダイヤモンド自己支持膜の研究の最近の進展
。- (英語
- 拘束ホットフィラメントCVD法によるダイヤモンド膜の作製に関する研究
ホットフィラメントCVD法は、装置が簡単で大面積成膜が可能であるなどの利点がある。しかし、成長速度が遅く、コストが高いため、普及にはまだ限界がある。ホットフィラメントCVD法でダイヤモンド膜を作製する際、成膜速度を向上させる方法として、バイアス電圧や高周波を印加する方法と、補助ガスを添加する方法がある。従来のホットフィラメントCVD法によるダイヤモンド膜の成膜速度は0.9~2.0μm/hである。バイアス電圧や高周波を印加することで、電子のエネルギーを高め、衝突確率を向上させ、プラズマ密度を高めて所望の成膜速度を達成することができる。この技術は、先進的なレーダーや通信システム、超高効率ハイブリッド自動車、極限環境における電子機器、次世代航空宇宙電子機器などへの応用が期待されています。
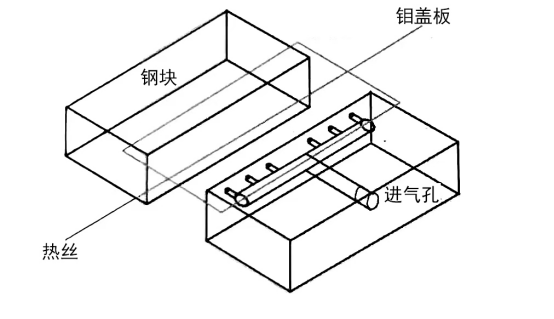
Figure 2: Constrained Space Deposition Model for Hot Filament CVD
自作の制約空間装置は、図2に示すように、高温フィラメントと反応ガスを狭いスリット空間内に閉じ込めます。高さの等しい2つの鋼鉄ブロックが拘束壁として基板ステージに平行に配置されている。拘束壁の上端は高融点Moプレート(融点2622±10℃)で覆われ、長さ8cm、幅3cm、高さ2.1cmの長方形のスリットが両側に開いている。高温のフィラメントはスリットを通り、基板はその真下に位置する。反応ガスは、均一なガス流分布を確保するために、多孔質ガス注入口を用いて側壁の注入口から制約された空間に導入される。
拘束蒸着法は、成長速度を効果的に向上させることができる。
拘束蒸着法は、成長速度を効果的に向上させることができる。その理由は、Dai Kai氏らによれば、次の3つの観点から説明できる。
エネルギー濃度:これは、高温フィラメントのエネルギー濃度とガスの強制フローエネルギーの両方を含みます。ホットフィラメントCVD法によるダイヤモンドの成膜では、高温フィラメントが成膜反応に必要なエネルギーのほとんどすべてを供給します。従来の方法では、反応空間が比較的大きいため、輻射や熱伝導によってフィラメントのエネルギーが著しく浪費される。これに対し、制約条件付き法では、同じ出力条件下でフィラメントのエネルギーを効果的に集中させることができる。さらに、より小さなスリット反応領域に反応ガスを導入することで、巨視的な強制流動が促進され、ガスの流動状態がより活発で複雑になり、ガスとフィラメントとの衝突頻度が増加するため、励起とクラッキングが促進される。反応性ガス種の輸送はより効率的になる。逆に、従来の方法におけるガス流状態は安定した層流であり、その結果、ガスのクラッキングと輸送効率は比較的低くなる。
反応ガスの濃度:
反応ガスの濃縮:従来の方法と比較して、スリットに入ったガスはフィラメントの効果的なクラッキング領域に直接送られるため、反応ガスがより濃縮される。フィラメントのエネルギー集中の条件下で、より効果的な反応粒子を励起し、クラッキングすることができる。
スリット内のガスの乱流効果:従来の方法と比較して、スリットで制約された空間の体積は減少し、制約壁のブロック効果と衝突効果、フィラメントの加熱膨張効果、真空ポンプの吸引効果により、スリットに入る気体はより大きな強制流動を受ける。その結果、スリット内に複雑で活発な乱流が形成される。ガスの旋回乱流状態は、フィラメントとの衝突を繰り返し、クラッキングを促進し、より高い粒子密度とエネルギーレベルをもたらす。さらに、基板との衝突頻度が高いため、基板表面の境界層が減少し、蒸着効果が向上する。制約のない蒸着法では、活性粒子のガス励起と輸送は効率的ではありません。
Source:Dai Kai、Research on the Preparation of Diamond Films by Constrained Hot Filament CVD Method、Diamonds and Abrasives Engineering、2018.4:1--5.
- MPCVDの多様性
- MPCVDデバイス構造の多様性
マイクロ波プラズマ化学気相成長法(MPCVD)の利点は、プラズマエネルギーがマイクロ波エネルギーによって維持され、放電プロセス中に金属電極が不要であるため、金属電極の使用による他のCVD成膜法で起こり得る汚染を回避できるという事実にある。さらに、MPCVD法のガス放電ゾーンは高濃度であるため、高密度のプラズマが生成されるだけでなく、より多くの反応種が励起される。放電プロセスは極めて安定しており、これらすべてが高品質ダイヤモンドの長期安定成長に寄与している。これらの利点により、国内外において、高品質のダイヤモンド単結晶や光学グレードの多結晶の製造方法として好まれています。
国際的な規制によると、MPCVD装置に使用可能なマイクロ波周波数は245GHzと915GHzです。2つの異なるマイクロ波周波数を比較すると、915 GHzの周波数は波長が長く、プラズマ球が大きくなるため、より高いマイクロ波電力を必要とします。この周波数で蒸着できるダイヤモンド膜は、245GHzマイクロ波の約2.67倍と、より大きな有効蒸着直径を持つ。これらの利点に基づき、915GHz MPCVD装置は、ダイヤモンド蒸着効率を大幅に改善し、ダイヤモンド材料の準備サイクルとコストを削減することができ、産業界にとって非常に魅力的な装置となる。しかし、915GHz MPCVD装置は、より高い電力を必要とし、その結果、より複雑な構造と細部が必要となり、装置開発、製造技術、およびコストに高い要求を課すことになる。現在、周波数245GHzと519GHzのMPCVD装置を用いた単結晶ダイヤモンドのバッチ調製の報告がある。しかし、ダイヤモンドの成膜環境は過酷であるため、プラズマによる石英のエッチングによる汚染を避けるために、石英管や石英ベルジャー型のMPCVD装置が採用されることは少ない。そこで、現在主流の単結晶ダイヤモンド作製装置を簡単に紹介する。
3.1 円筒共振器型MPCVD装置
1992年頃、アメリカのASTeX社が石英ベルジャー型MPCVDの研究をもとに、図3に示すような円筒共振器型MPCVD装置を開発した。この装置は、石英ベルジャーを石英窓に置き換え、金属共振器が成膜室として機能するようにしたものである。共振器自体は冷却水を用いて冷却されるため、マイクロ波の使用電力が効果的に増加する。さらに、プラズマが石英窓をエッチングするリスクを避けるため、石英窓は通常プラズマ球から離れた位置に配置される。しかし、これは、特にマイクロ波出力が高く圧力が低い条件下では、二次電界の領域で二次プラズマ球の発生につながる可能性がある。石英をエッチングする危険性が再浮上し、過大な出力は二次プラズマの直接加熱効果により石英窓を損傷させる可能性がある。これらの現象により、2.45GHz円筒共振器MPCVDデバイスの実用的なパワーは、一般的に5kWを超えない。それにもかかわらず、この装置の利点は真空性能が保証しやすいことにあり、その技術は比較的成熟しているため、高品質の単結晶ダイヤモンドを作製するための主流装置の一つとなっている。しかし、出力とチャンバー構造の制限から、この装置の有効蒸着直径は約2インチであり、円筒共振器MPCVD装置の応用の見通しに一定の制約を課している。
図3: 円筒形共振器MPCVD装置
3.2 アニュラーアンテナ MPCVD 装置
最初の設計スキーム
初期の設計スキームは、図 4 に示すように、アメリカの ASTeX 社の Besen らによって特許で提案されました。金属共振器MPCVD装置と比較して、この装置の最も大きな特徴は、マイクロ波の入力方法の変更であり、単純な同軸アンテナの代わりに環状アンテナによって完成されています。マイクロ波の伝送モードもシングルモードから、TM012やTM013のようなマルチモード形式にシフトしており、そのため、この種のデバイスは多くの文献でマルチモード共振器MPCVDデバイスと呼ばれています
。さらに、環状アンテナMPCVD装置の主な利点は、その石英窓が本質的にプラズマと接触していないため、石英のエッチングによる汚染を避けることができることです。チャンバーの構造上、この装置では二次プラズマの問題も発生しない。円筒形共振器MPCVD装置と比べると、プラズマ球の安定性を確保しやすい。さらに、独自のチャンバー設計により、この装置で生成されるプラズマ球は平坦化され、その結果、円筒形共振器よりも温度分布が均一になり、大型単結晶ダイヤモンドのバルク成長に適している。
しかし、この装置にも欠点がある。アンテナと基板ステージシステムが一体化した構造であるため、基板ステージの補助的な調整、特に基板ステージの仰角調整が難しい。現在、2.45 GHz周波数の環状アンテナMPCVD装置の実際の入力パワーは6~10 kWのレベルに達することができ、一方、915 MHz周波数の装置の実際のパワーは100 kWに達することができる。円筒形共振器MPCVD装置と比較すると、マイクロ波の最大入力パワーとプラズマ球の大きさの両方が大幅に向上しており、ダイヤモンド膜成膜に適した装置の1つとしてさらに促進されている。
図4: アニュラーアンテナMPCVD装置
3.3 同軸ブレード MPCVD 装置
同軸ブレード MPCVD 装置
同軸ブレード MPCVD 装置は、環状アンテナ装置と同様の原理で動作しますが、マイクロ波源が TM01 モードマイクロ波を利用する点が主に異なります。プラズマは、リアクターの上部にある同軸ブレードの周りに形成され、サンプル基板に対して放電します(図5に示すように)。環状アンテナ装置と比較して、この設計では基板ステージが自由になり、基板ステージの高さ変更によってプラズマ球の形状を調整できるため、長期的なダイヤモンド成長に有益である。
図 5: 同軸ブレード MPCVD 装置
図 5: 同軸ブレード MPCVD 装置
図 5: 同軸ブレード MPCVD 装置
3.4 楕円共振器 MPCVD 装置
楕円共振器 MPCVD 装置
楕円共振器 MPCVD 装置が最初に登場したのは 1997 年頃で、図 6 に示すように、ドイツのフラウンホーファー研究所によって設計・開発されました。図から、楕円共振器 MPCVD 装置の構造は、石英ドーム MPCVD 装置のそれと非常によく似ていることが観察できます。どちらも大きな石英ドームを持ち、マイクロ波モード変換の手段として同軸アンテナコンバーターを採用しています。両者の明らかな違いは、共振器の構成にある。楕円共振器MPCVD装置は、楕円の焦点にマイクロ波が収束する原理を巧みに利用している。マイクロ波は上部の焦点アンテナから放射され、基板ステージの下部焦点に収束するため、高エネルギー密度のプラズマ球が実現する。さらに、金属楕円のサイズが大きいため、より大きな石英ドームを装備することができ、プラズマ球と石英材料との間の安全な距離を効果的に維持し、エッチング汚染を防ぐことができる。このような装置のマイクロ波入力パワーは、一般的に10kWかそれ以上のレベルに達することができます。
まとめると、高品質の単結晶ダイヤモンドを作製するための前提条件は、クリーンな成長環境を提供することであり、装置チャンバーの合理的な設計が特に重要になります。一方、MPCVD装置は、より高い出力要求に応えるべく、改良と研究開発が続けられている。高出力条件では、プラズマのエネルギー密度が大きくなり、プラズマ球のサイズが大きくなるため、高品質な大型単結晶の高速バルク成長に適している。この高出力条件の追求が、MPCVD技術開発の原動力となっている。