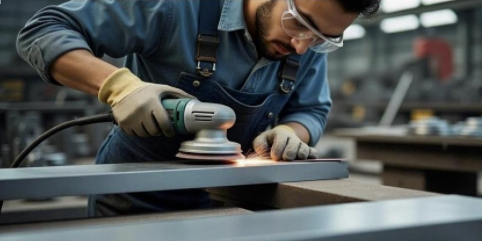
Table of Contents
Deburring is a common issue in metal processing. No matter how advanced or precise the equipment, burrs are inevitably formed along with the product. Burrs are excess metal scraps generated at the edges of the material due to plastic deformation during processing. This is especially common in materials with good ductility or toughness. Below, let's take a closer look at methods for deburring.
Burr types mainly include flanged burrs, sharp-edged burrs, splashes, and other protruding excess metal remnants that do not meet product design requirements. Up until now, no effective method has been developed to completely eliminate burrs during the production process. Therefore, engineers focus on post-processing deburring techniques to ensure the design requirements are met. Many different deburring methods and equipment have been developed for different products.
Generally, deburring methods can be classified into four categories:
1.Rough Level (Hard Contact)
This category includes cutting, grinding, filing, and scraping processes.
2.Intermediate Level (Soft Contact)
This category includes abrasive belt grinding, polishing, elastic grinding wheels, and other polishing methods.
3.Precision Level (Flexible Contact)
This category includes flushing, electrochemical processing, electrolysis grinding, and rolling processes.
4.Super Precision Level (Precision Contact)
This category includes abrasive flow deburring, magnetic polishing deburring, electrochemical deburring, thermal deburring, and intense ultrasonic deburring, which provide the necessary precision for part processing.
When choosing a deburring method, several factors need to be considered, such as the material characteristics of the part, its structure, size, and precision requirements. Special attention should be given to surface roughness, dimensional tolerance, deformation, and residual stress.
Electrolytic Deburring
Electrolytic deburring is a chemical deburring method that can remove burrs from mechanical, grinding, and stamping processes while rounding off or chamfering sharp edges of metal parts. This electrochemical method, known as Electrolytic Deburring (ECD), involves positioning a tool cathode (usually brass) near the burr area of the workpiece. There is a specific gap between the two (generally 0.3–1 mm). The conductive portion of the tool cathode aligns with the burr edge, while the rest of the surface is covered by insulation to concentrate the electrolysis action on the burr part.
During processing, the tool cathode is connected to the negative terminal of a DC power supply, and the workpiece is connected to the positive terminal. A low-pressure electrolyte (typically sodium nitrate or sodium chloride solution) flows between the workpiece and cathode under a pressure of 0.1–0.3 MPa. Upon activation of the DC power supply, the burrs dissolve through anodic action and are removed by the electrolyte.
Electrolyte solutions are mildly corrosive, so the workpiece must undergo cleaning and rust prevention treatment after deburring. Electrolytic deburring is suitable for removing burrs from hidden or intricate areas of parts, such as cross-holes or complex shapes. It is highly efficient, typically taking only a few seconds to several tens of seconds for deburring. This method is commonly used for deburring gears, splines, connecting rods, valve bodies, and crankshaft oil passage holes, as well as rounding sharp edges. However, a disadvantage is that the area around the burr may also be affected by electrolysis, potentially losing its original surface luster and affecting dimensional precision.
In addition to electrolytic deburring, there are several other specialized deburring methods:
- Abrasive Flow Deburring
Abrasive flow machining technology is a new deburring process developed abroad in the late 1970s, especially suitable for burrs that have just entered the finishing stage. However, it is not suitable for small, long holes or metal molds with blind holes. - Magnetic Polishing Deburring
This method originated in the Soviet Union, Bulgaria, and other Eastern European countries in the 1960s. By the mid-1980s, Japanese researchers conducted in-depth studies on its mechanism and applications.
In magnetic polishing, the workpiece is placed within a magnetic field created by two magnetic poles. Magnetic abrasives are inserted into the gap between the workpiece and magnetic poles. Under the influence of the magnetic field, the abrasives align along the lines of magnetic force, forming a soft yet rigid magnetic polishing brush. As the workpiece rotates and undergoes axial vibration within the magnetic field, the abrasives move relative to the workpiece, performing polishing and deburring.
Magnetic polishing is an efficient and fast method for deburring and polishing parts, suitable for various materials, sizes, and structures. It is a cost-effective, high-efficiency, versatile, and high-quality finishing method.
Currently, the industry uses this method for polishing and deburring the inner and outer surfaces of rotating bodies, flat parts, gear teeth, complex profiles, and for removing oxide scales from wire rods, cleaning printed circuit boards, etc. - Thermal Deburring
Thermal Deburring (TED) uses the high temperatures generated by the combustion of hydrogen-oxygen gases or a mixture of oxygen and natural gas to burn off the burrs. Oxygen and oxygen or natural gas and oxygen are introduced into a sealed container, and after ignition by a spark plug, the mixed gases explode instantaneously, releasing large amounts of heat energy to remove the burrs. After combustion, oxidation powders may adhere to the surface of the workpiece, which requires cleaning or acid washing. - High-Intensity Ultrasonic Deburring
High-intensity ultrasonic deburring technology has become popular in recent years. Its cleaning efficiency is 10 to 20 times that of regular ultrasonic cleaning machines. Cavitation is evenly distributed in the water tank, enabling ultrasonic waves to complete the process without the need for cleaning agents, usually within 5 to 15 minutes.
Below, we have listed the 10 most common deburring methods:
- Manual Deburring
This is a commonly used method in many businesses, involving tools such as files, sandpaper, and grinding heads. Files can be manual or pneumatic.
The labor cost is high, and the efficiency is not very good. It is also difficult to remove burrs from complex cross-holes. The technical requirements for workers are not high, making it suitable for parts with small burrs and simple structures. - Punching Die Deburring
This method involves using a punching die in combination with a punching machine to remove burrs.
It requires the creation of a punching die (rough die + fine punching die), and possibly also requires a shaping die. It is suitable for parts with relatively simple splitting surfaces, and the efficiency and deburring effect are better than manual methods. - Grinding Deburring
This method includes vibration, sandblasting, and drum methods, which are commonly used by companies.
There may be issues with incomplete burr removal, and subsequent manual treatment or combining with other methods may be required. It is suitable for large-batch small products. - Cryogenic Deburring
This method uses low temperatures to rapidly embrittle burrs, followed by the use of abrasive media to remove the burrs.
The equipment cost is about 200,000 to 300,000 yuan, and it is suitable for products with small burrs and thin wall thickness. - Thermal Explosion Deburring
Also known as thermal deburring or explosive deburring. This method involves introducing flammable gases into a furnace and allowing the gases to explode under specific conditions, using the energy from the explosion to dissolve and remove the burrs.
The equipment is expensive (over a million yuan), the technical requirements are high, and the efficiency is low. It also has side effects such as rusting and deformation. This method is primarily used in high-precision fields such as automotive and aerospace for small, delicate components. - Engraving Machine Deburring
The equipment is relatively inexpensive (tens of thousands of yuan) and suitable for products with simple spatial structures and regular deburring locations. - Chemical Deburring
This method uses electrochemical reaction principles to automatically and selectively remove burrs from parts made of metal materials.
It is suitable for difficult-to-remove internal burrs, such as fine burrs (less than 0.07 mm) on pump bodies, valve bodies, etc. - Electrolytic Deburring
This electrochemical method uses electrolytic action to remove burrs from metal parts.
The electrolyte has a certain corrosive effect, and the area near the burr is also affected by electrolytic action, causing the surface to lose its original luster and potentially affecting dimensional precision. After deburring, the parts must undergo cleaning and rust prevention treatment. Electrolytic deburring is suitable for removing burrs from hidden or complex areas such as cross-holes or intricate shapes. It is highly efficient, with deburring typically taking only a few seconds to several tens of seconds. This method is commonly used for deburring gears, connecting rods, valve bodies, crankshaft oil passages, and rounding sharp edges. - High-Pressure Water Jet Deburring
This method uses water as a medium, utilizing its instantaneous impact force to remove burrs and flash produced during processing, while also achieving cleaning.
The equipment is expensive and is mainly used in critical parts of automobiles and hydraulic control systems in construction machinery. - Ultrasonic Deburring
Ultrasonic waves create instantaneous high pressure to remove burrs.
This method is primarily used for microscopic burrs. If the burrs need to be observed under a microscope, ultrasonic methods can generally be used for their removal.