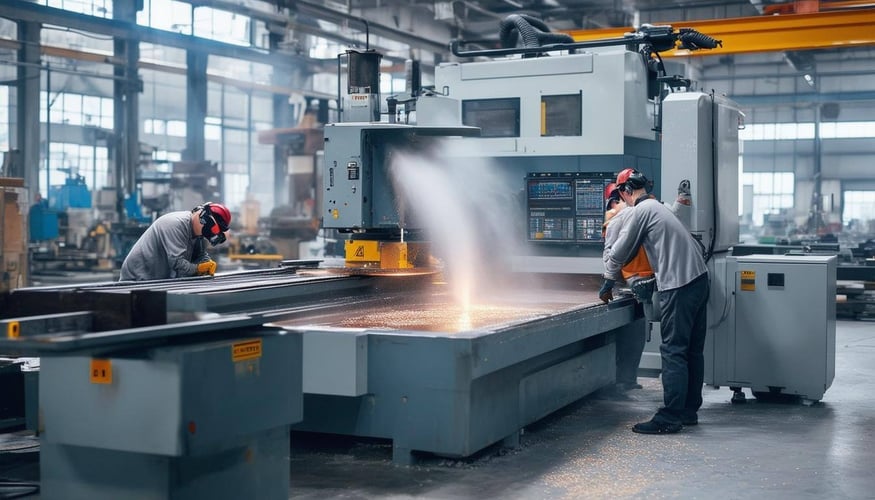
Table of Contents
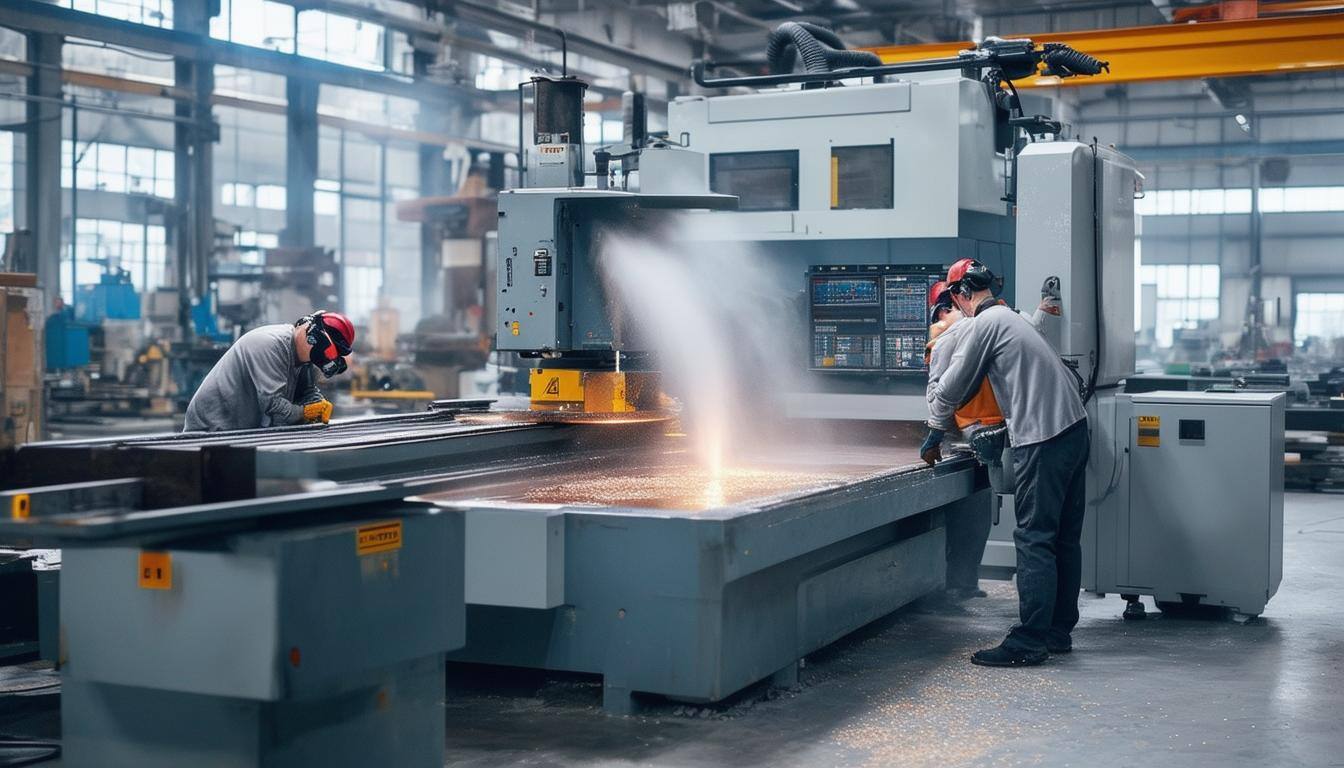
Introduction to Grinding Methods
Grinding is a critical process in precision finishing, utilized to achieve high accuracy and fine surface finishes on various materials. This technique involves the use of abrasive particles to remove material from a workpiece, thereby refining its surface. The grinding process can be categorized into three primary methods: wet grinding, dry grinding, and semi-dry grinding. Each method has its unique applications, benefits, and specific use cases, making it essential to understand their differences to select the appropriate one for your needs.
Applications of Wet Grinding in Precision Finishing
Wet grinding, also known as sand-coated grinding, involves the continuous injection or coating of a liquid abrasive on the grinding surface. This method is primarily used for coarse grinding, where the abrasive particles slide and roll between the workpiece and the grinding tool, creating a cutting motion. The liquid medium helps reduce friction and heat generation, which can be beneficial for delicate materials that might be susceptible to thermal damage.
Wet grinding is particularly effective for materials that require a large amount of material removal in a short period. It's commonly used in the initial stages of the grinding process to quickly bring a workpiece to near-final dimensions. Industries such as automotive, aerospace, and heavy machinery often rely on wet grinding for its efficiency and ability to handle tough materials.
Advantages and Uses of Dry Grinding
Dry grinding, also known as sand-embedded grinding, involves pressing and embedding the abrasive particles into the surface of the grinding tool. Unlike wet grinding, this method requires only a small amount of auxiliary materials, such as stearic acid mixed fat, to be applied to the grinding tool. Dry grinding is typically used for fine grinding, where precision and surface finish are critical.
The main advantage of dry grinding is its ability to achieve high levels of accuracy and fine surface finishes, often reaching surface roughness levels as low as Ra0.01 microns. This method is ideal for applications where the final dimensions and surface quality of the workpiece are paramount. Industries that manufacture high-precision components, such as semiconductor equipment, medical devices, and precision instruments, frequently use dry grinding to meet their stringent quality standards.
Exploring Semi-Dry Grinding Techniques
Semi-dry grinding is a hybrid technique that combines elements of both wet and dry grinding. In this method, a paste-like abrasive is used, which provides some of the lubricating and cooling benefits of wet grinding while maintaining the precision and control of dry grinding. Semi-dry grinding can be performed manually or with the aid of a grinder, making it a versatile option for various applications.
One of the key benefits of semi-dry grinding is its ability to handle a wide range of materials with varying hardness levels. The paste abrasive allows for controlled material removal, making it suitable for both coarse and fine grinding tasks. This method is often used in applications where a balance between material removal rate and surface finish is required, such as in the production of complex geometries and intricate profiles.
Comparative Analysis of Grinding Methods
When comparing wet, dry, and semi-dry grinding methods, several factors need to be considered, including material type, desired surface finish, and production efficiency. Wet grinding is highly effective for rapid material removal and is best suited for initial grinding stages. Its cooling properties help prevent thermal damage, making it ideal for heavy-duty applications.
Dry grinding, on the other hand, excels in achieving fine surface finishes and high precision. Its ability to produce extremely smooth surfaces makes it the go-to method for finishing high-precision components. However, it may not be as efficient as wet grinding in terms of material removal rate.
Semi-dry grinding offers a middle ground, providing both cooling and precision benefits. This method is versatile and can be adapted to various grinding tasks, making it a valuable option for applications that require a balanced approach.
Choosing the Right Grinding Method for Your Needs
Selecting the appropriate grinding method depends on several factors, including the material being processed, the required surface finish, and the specific application. For tasks that require rapid material removal and can benefit from cooling, wet grinding is the optimal choice. Industries dealing with tough, heat-sensitive materials will find this method particularly advantageous.
For applications where precision and surface quality are critical, dry grinding is the preferred method. Its ability to produce fine finishes makes it ideal for high-precision components and intricate profiles. Industries such as semiconductor manufacturing and medical device production often rely on dry grinding to meet their stringent quality standards.
Semi-dry grinding is suitable for applications that require a balance between material removal and surface finish. Its versatility allows it to handle a wide range of materials and grinding tasks, making it a valuable option for various industries.
Conclusion
Understanding the different grinding methods—wet, dry, and semi-dry—is essential for optimizing precision finishing processes. Each method offers unique benefits and applications, making it crucial to select the appropriate one based on your specific needs. Whether you require rapid material removal, high precision, or a balanced approach, mastering these grinding techniques will help you achieve superior results in your finishing processes.