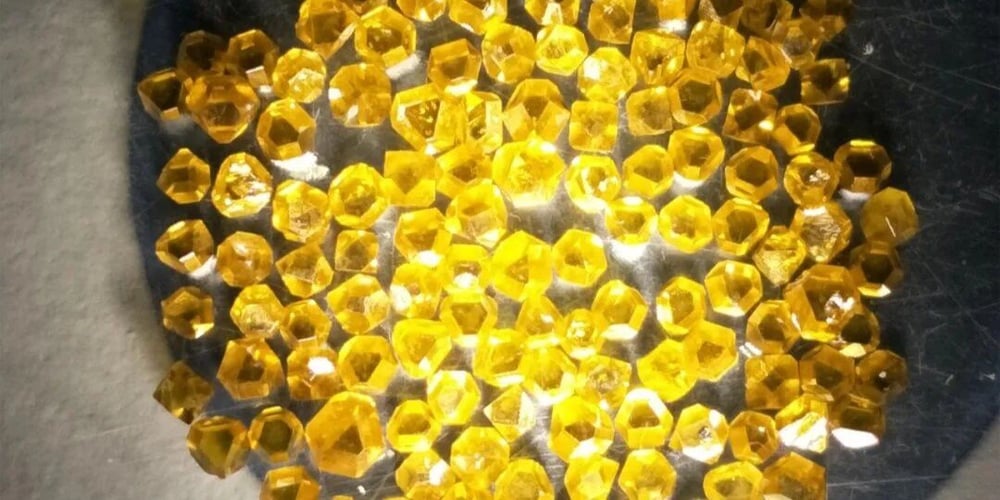
Table of Contents
By Wang Guangzu (Zhengzhou Research Institute for Abrasives & Grinding),
Wang Yun (Central China Diamond Tool Manufacturing Co., Ltd.),
Qin Yu (Henan Eagle Abrasives & Grinding Co., Ltd.)
Diamond is a material that integrates superior physical, chemical, and mechanical properties. Over the past few decades, its exceptional hardness and excellent wear resistance have been extensively utilized—enabling its widespread application in the form of abrasives, grinding tools, and cutting tools across industries such as machinery, petroleum, automotive, aerospace, and semiconductor processing, playing an irreplaceable role. In fact, diamond also exhibits outstanding electrical, optical, thermal, and acoustic properties, which have yet to be fully explored and developed.
Diamond possesses excellent electrical characteristics, including an ultra-wide bandgap, extremely high breakdown field strength, and high electron and hole mobility, making it a promising candidate as the ultimate semiconductor. Acoustically, diamond features the highest surface acoustic wave velocity and an extremely high Young’s modulus among all known materials. Optically, it is transparent to photons from the far-infrared to ultraviolet range (below the bandgap energy). Thermally, diamond has a thermal conductivity that surpasses that of copper. These attributes give diamond significant potential for cross-disciplinary applications.
1. Radioactive Diamond Batteries That Can Generate Power for Thousands of Years
The prototype of nuclear batteries can be traced back to the 1913 experiments of British physicist Henry Moseley, who demonstrated the process of generating electric current using radiation. During the 1950s and 1960s, the aerospace industry explored applying Moseley’s research to spacecraft to improve long-term power supply. At the time, some companies were also studying the use of nuclear batteries in devices like radio receivers.
However, this type of nuclear battery still faced limitations in terms of safety and electrical conductivity. In this regard, the advent of synthetic diamond provided a promising solution. Diamond is one of the hardest known materials and can be engineered through special processes to be either radioactive or to function as a semiconductor.
Nuclear batteries are powered by the beta decay of nuclear waste. Beta decay occurs when a radioactive nucleus (composed of protons and neutrons) releases excess particles in an effort to reach a stable proton-to-neutron ratio, emitting large quantities of beta particles (high-energy electrons or positrons) in the process.
When beta particles strike a semiconductor material, they generate an electric current, which is then converted into usable energy. However, because beta particles are emitted in random directions, only a limited number can strike the semiconductor, resulting in low energy output and limited efficiency.
Radioactive diamond batteries are made using Chemical Vapor Deposition (CVD), a technique widely used in the production of synthetic diamond. Researchers modified the CVD process by introducing radioactive methane containing carbon-14 isotopes, thereby producing radioactive diamond. The embedded nuclear waste acts as the fuel source, and under beta radiation, the battery can provide long-term energy output without the need for recharging.
“Carbon-14 was chosen because it emits short-range radiation that is quickly absorbed by any solid material,” explained Professor Neil Fox.
However, the team from the University of Bristol noted that their radioactive battery—containing 1 gram of carbon-14—produces only a few microwatts of power, which is significantly less than a typical AA battery. As a result, current applications are limited to small, low-power devices such as sensors and pacemakers, and are not yet suitable for laptops or smartphones.
It is worth noting that the radioactive diamond battery developed by the Bristol research team is being prepared for commercialization by the British company Arkenlight. The company’s first miniature battery product was expected to launch in the second half of 2023. (Source: Tencent News)
2. Diamond and Silicon Carbide Substrate Thermal Management Technology
This cooling technology enables the efficient dissipation of heat from high-power GaN high electron mobility transistors (HEMTs), allowing power amplifiers to operate stably at high output levels.
High-frequency GaN-HEMT power amplifiers have already been applied in radar and radio communication for long-distance wireless transmission. They are also expected to be used in weather radar systems to observe localized heavy rainfall and in emerging 5G millimeter-wave communication protocols. For radar and radio systems operating in the microwave to millimeter-wave frequency bands, increasing the output power of the GaN-HEMT power amplifiers used for signal transmission can extend the transmission range of radio waves. This can significantly broaden the radar's observational scope and enhance the capacity and reach of communications.
Although silicon carbide (SiC) substrates have relatively high thermal conductivity, devices with increasing power output require substrates with even better thermal performance to effectively transfer heat to cooling structures. Single-crystal diamond, with a thermal conductivity nearly five times higher than that of SiC, is recognized as a highly efficient thermal management material.
To bond single-crystal diamond to devices used for cooling, conventional manufacturing processes employ argon (Ar) ion beams to remove surface impurities. However, this often results in the formation of a low-density damaged layer on the surface, which weakens the bond strength of the single-crystal diamond. Additionally, when using insulating films such as SiN for bonding, thermal resistance introduced by the SiN layer compromises overall heat dissipation performance.
To prevent the formation of damage layers on the diamond surface caused by Ar ion beam exposure, Fujitsu has developed a technique that protects the surface with an ultra-thin metallic film prior to ion beam treatment. To ensure surface planarity (essential for effective room-temperature bonding), the metal film must be limited to a thickness of 10 nm or less.
This method has been proven to prevent damage layer formation after Ar beam exposure, thereby enhancing bond strength and enabling single-crystal diamond to be bonded to SiC substrates at room temperature.
As a result, this technology can be used to produce GaN-HEMT power amplifiers with higher output power. When applied to systems such as weather radar, the GaN-HEMT amplifiers used in transmitters are expected to extend the radar’s observable range by 1.5 times. This improvement would allow faster detection of cumulonimbus clouds capable of producing sudden downpours, supporting better disaster prevention readiness.
(Source: China Automation Network)
3. Nanodiamond Thermal Grease Doubles Thermal Conductivity
As a thermal interface material between the CPU and heat sink, thermal grease plays a critical role in heat dissipation. Conventional thermal grease typically offers a thermal conductivity around 10 W/(m·K). The company Inex has introduced a nanodiamond thermal grease with a thermal conductivity of up to 17 W/(m·K), effectively doubling the heat dissipation performance. It also maintains stability at high temperatures up to 350 °C.
This thermal grease, model JP-DX2, is claimed to be manufactured using nanotechnology-based high-quality diamond thermal conductive materials, forming a fine molecular structure that delivers excellent thermal conductivity, reaching 17 W/(m·K).
What does this mean in practice? Common thermal greases generally have thermal conductivities below 10 W/(m·K), with many ranging from 7 to 8 W/(m·K). High-quality variants can reach 10 to 13 W/(m·K). Currently, the best-performing thermal interface materials are liquid metals, which easily exceed 70 W/(m·K), with some even surpassing 100 W/(m·K)—representing 5 to 10 times the performance of standard greases.
The nanodiamond thermal grease essentially doubles the heat transfer capacity. As a crucial interface between the CPU and heat sink, this type of thermal grease significantly improves cooling efficiency.
In addition to its superior thermal conductivity, JP-DX2 grease also features excellent chemical stability—it is non-corrosive, oxidation-resistant, non-toxic, and has low volatility. It has a shelf life of 3 years before use, and a service life of up to 4 years after application. The operational temperature range is also extremely broad, spanning from -150 °C to 350 °C, with a recommended usage range from -140 °C to 340 °C—far beyond the thermal demands of typical CPU cooling systems.
(Source: Fast Technology)
4. N-Type Conductive Channel Diamond Field-Effect Transistor
A research team from the United States’ National Institute for Materials Science (NIMS) has developed the world’s first metal-oxide-semiconductor field-effect transistor (MOSFET) driven by a diamond-based n-type channel. This breakthrough holds significant implications for monolithic integration—i.e., integrating multiple devices within a single semiconductor substrate—as represented by conventional integrated circuits (ICs). It also marks a critical step forward in realizing environmentally robust complementary metal-oxide-semiconductor (CMOS) integrated circuits using diamond, and in advancing diamond’s application in power electronics.
Diamond semiconductors possess exceptional material properties, including an ultra-wide bandgap (5.45 eV), high breakdown electric field (10 MV/cm), high carrier saturation drift velocity, and superior thermal conductivity (22 W/cm·K), along with an excellent device quality factor. With diamond as the substrate, it is possible to develop electronic devices that operate under high temperature, high frequency, high power, and radiation-resistant conditions—effectively overcoming technical bottlenecks such as self-heating and avalanche breakdown. Diamond semiconductors have played a key role in the development of 5G/6G communication systems, microwave/millimeter-wave integrated circuits, and detection and sensing technologies. In particular, under extreme conditions—such as high temperatures or high radiation environments near reactor cores—diamond semiconductors demonstrate outstanding performance and reliability. Therefore, diamond semiconductors are widely recognized as one of the most promising next-generation semiconductor materials and have earned the title of the “ultimate semiconductor material” globally.
In recent years, with advances in diamond growth technology, power electronics, spintronics, and microelectromechanical systems (MEMS) sensors capable of operating under high temperature and strong radiation, there has been a growing demand for monolithic integration of peripheral circuits based on diamond CMOS devices. To leverage diamond’s exceptional properties and realize integrated circuits for highly stable environmental control systems, high-power CMOS is eagerly anticipated. However, the fabrication of CMOS integrated circuits requires both p-type and n-type channel MOSFETs.
Currently, while diamond semiconductor fabrication has reached a relatively mature stage, achieving n-type doping in diamond remains a major global challenge. For years, researchers have explored suitable dopant elements and methods for achieving low-resistivity n-type diamond through both theoretical simulations and experimental approaches—but with limited success. A key reason lies in the fact that most of the earlier studies were based on silicon single-crystal doping theories, which do not effectively translate to diamond.
Primary impurity elements explored include boron, phosphorus, sulfur, and lithium. These have been introduced into single-crystal or microcrystalline diamond films either during growth or via ion implantation. However, the resulting films typically exhibit low electrical conductivity and poor electron mobility, making them unsuitable for use in electronic devices. For example, nitrogen forms a deep-level impurity in diamond, with an activation energy of 1.7 eV at room temperature, which severely limits the availability of free carriers. While phosphorus has a shallower energy level, it also suffers from weak carrier conductivity at room temperature. Once incorporated into diamond, phosphorus readily forms phosphorus-vacancy complexes, which prevent the release of free electrons. To date, no suitable donor impurity has been identified.
From this perspective, the development of a new doping theory tailored specifically to diamond semiconductors is urgently needed.
(Source: DT Semiconductor)
5. Breakthrough in Polycrystalline Diamond Heterogeneous Integration Technology
The team led by Liu Xinyu at the Institute of Microelectronics, Chinese Academy of Sciences, has made significant progress in the direct bonding technology between thick-film GaN and polycrystalline diamond. They not only overcame the challenge of the surface morphology of polycrystalline diamond, but also achieved high-efficiency direct bonding with thick-film GaN at room temperature—paving a new path for the development and application of wafer-level polycrystalline diamond bonding technology.
Using advanced Dynamic Plasma Polishing (DPP) technology, the team significantly reduced the height of surface asperities on polycrystalline diamond to 1.2 nm, achieving an ultra-smooth surface with a roughness of only 0.29 nm. Based on this, and employing a surface-activated bonding method, they successfully achieved room-temperature direct bonding of a 370 μm-thick GaN layer to a ~660 μm-thick polycrystalline diamond substrate. The bonding yield reached an impressive 92.4%, and the structure can stably operate across a wide temperature range from -55°C to 250°C.
In recent years, GaN/diamond heterogeneous integration technology has gained wide attention for its great potential in fabricating high-reliability, high-power-density GaN-based high electron mobility transistors (HEMTs). Among available methods, wafer direct bonding stands out due to its advantages of high interfacial thermal conductivity and low thermal stress, showing promising applications in materials and device integration. However, the extremely stringent requirements on surface flatness and roughness pose a key limitation to further advancement.
Although single-crystal diamond can achieve low surface roughness and high flatness via chemical mechanical polishing (CMP), challenges in growing large-size single-crystal diamond and its high cost hinder its practical use. In contrast, polycrystalline diamond offers advantages such as low cost and large size, but its complex and non-uniform surface morphology makes it difficult for CMP to meet direct bonding requirements. Meanwhile, thick-film GaN also encounters stress issues during bonding, further increasing the technical difficulty.
The use of dynamic-angle plasma polishing technology marks a breakthrough in resolving the surface morphology challenges of polycrystalline diamond. This technique allows for precise surface treatment of polycrystalline diamond without applying pressure, significantly reducing both surface roughness and peak height. Combined with an in-situ ion beam surface activation bonding method assisted by a silicon nanolayer, the team realized successful heterogeneous integration of thick-film GaN and polycrystalline diamond, achieving a bonding rate as high as 92.4%.
Using variable-temperature Raman spectroscopy, the team further investigated the residual stress variation at the GaN/diamond bonding interface over a wide temperature range. Results showed that approximately 200 MPa of residual stress existed at room temperature, and that the interfacial stress increased asymmetrically with temperature. This is primarily due to the similar coefficients of thermal expansion (CTEs) between GaN and the silicon nanolayer, and the large CTE mismatch between diamond and the silicon nanolayer. This asymmetric stress distribution further confirms the effectiveness of the amorphous silicon nanolayer as a buffer in stress relief.
(Source: China Superhard Materials Network)
6. Development of Superconducting Materials Using Diamond and Niobium
Russian scientists have discovered that one effective method to enhance diamond’s adhesive properties is to use tungsten to strengthen the bonding between diamond and transition metals. A major focus of diamond technology research is the metallization of diamond surfaces, which grants the material new properties such as superconductivity, improved thermal stability, better wettability, and the retention of its inherent physical and chemical characteristics.
However, diamond faces two key limitations: the difficulty of synthesizing large-grain diamond substrates, and poor adhesion between metal contacts and the diamond surface.
One of the most effective ways to metallize diamond is through sintering with metals such as titanium, chromium, tantalum, and zirconium. These metals form a layer of metal carbide upon contact with carbon. Niobium was selected in this study due to its ability to form chemically stable and reinforced thin films on the diamond surface. Researchers attempted to create a superconductor on the diamond surface, and found that when niobium is deposited onto the surface and heated, a phase transformation occurs. Upon heating, the film transitions into Nb₂C, and with further heating above 1200°C, niobium carbide (NbC) forms.
The stable crystal structure of niobium carbide depends on the density of carbon defects—which are relatively common under laboratory conditions. Theoretical calculations indicate that synthesizing NbC on the diamond surface can yield high-quality niobium carbide with lattice parameters close to those of defect-free materials. Calculations on the superconducting properties of NbC suggest a superconducting phase transition occurs at around 1940°C, which closely matches experimental measurements. The results also show that the quality of the niobium thin films produced is very high.
Notably, compared to other niobium-based alloys, the NbC films obtained exhibit low defect density while maintaining sufficient electronic diffusivity. This characteristic, coupled with observed superconductivity, has practical implications for the development of electronic detection devices. Researchers have confirmed that the synthesized NbC layers exhibit superconducting properties.
By covering diamond surfaces with such thin films and leveraging diamond’s high thermal conductivity, it becomes possible to develop ultra-sensitive detectors. Diamond's superior heat conduction greatly aids in signal detection, offering significantly faster response than other materials.
(Source: Shanghai Metals Market)