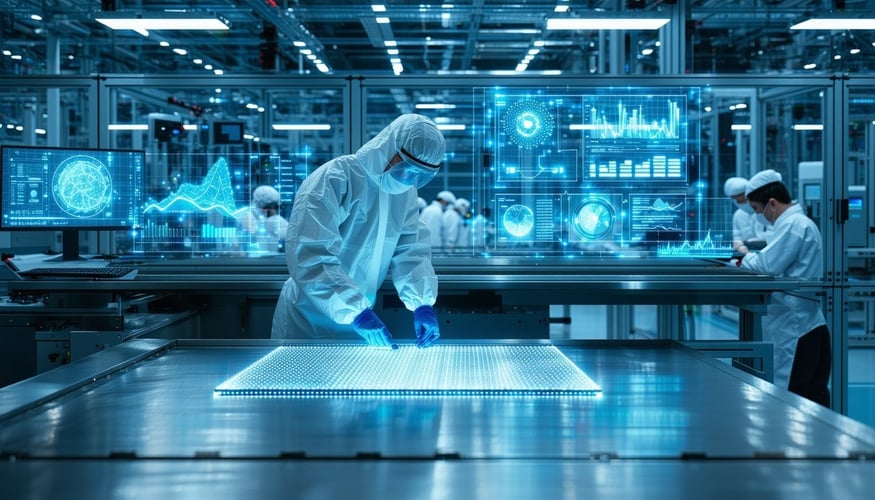
Table of Contents
According to Business Wire, semiconductor materials company ChEmpower recently announced the completion of an $18.7 million Series A funding round. The company focuses on providing polishing pads and chemical solutions for planarization processes. The funds will be used to scale its technologies in advanced chip manufacturing and packaging.
ChEmpower is reshaping semiconductor fabrication with its abrasive-free planarization technology. Its polishing pads and chemical solutions enable defect-free, ultra-flat surface finishing, enhancing chip yield and performance. Unlike traditional chemical mechanical planarization (CMP), which relies on abrasives and can leave behind scratches and particle residues that reduce yield and increase cost, ChEmpower’s solution simplifies the planarization process, lowers embedded costs, and supports sustainability through water reclamation—particularly crucial as planarization accounts for about 40% of water usage in semiconductor fabs.
Dr. Sudhanshu Misra, ChEmpower’s Co-founder and CEO, stated:
"The explosive growth of AI and the pressing demand for sustainable, high-performance semiconductors create a unique opportunity for ChEmpower. This funding will accelerate our operations, expand our market reach, optimize our product portfolio, and ensure our leadership in next-generation chip manufacturing."
As demand for high-performance AI chips soars, challenges in manufacturing, bandwidth, and advanced packaging continue to grow—especially as chips shrink in size and grow more complex in architecture. Currently, 40% of global wafer output comes from sub-10nm nodes. As nodes continue to shrink, more planarization steps are required to ensure performance. ChEmpower’s abrasive-free technology is playing a key role in enabling sub-10nm chip production and advancing next-generation AI and high-end semiconductor applications.
Quick Take:
ChEmpower’s signature abrasive-free planarization technology eliminates the need for conventional abrasive methods, offering clear advantages in yield improvement, defect reduction, and water/resource efficiency. It’s especially suitable for advanced nodes, AI chips, and cutting-edge packaging.
This presents a challenge to traditional CMP techniques, but also opens doors for transformation within the conventional grinding industry.
How the Traditional Grinding Industry Can Respond
Integration, not Replacement
Abrasive-free planarization is not a total rejection of grinding. Traditional CMP still holds irreplaceable value in semiconductor manufacturing—offering cost control, equipment versatility, and decades of process refinement. However, to remain relevant in high-end applications, traditional players must adapt. One path forward is hybrid workflows: using traditional grinding in coarse planarization stages, while incorporating abrasive-free solutions in the fine finishing phase.
Targeting Differentiated Markets
Abrasive-free technologies are currently focused on advanced nodes (sub-10nm), whereas traditional CMP continues to thrive in mature process nodes, packaging, and memory manufacturing. Grinding companies can strengthen their position in these segments while upgrading their offerings toward higher precision and lower damage.
Green Transformation to Lower Environmental Costs
ChEmpower’s emphasis on sustainability and water recovery highlights a direction traditional grinding should follow. Enhancing slurry recycling, reducing consumables, and improving waste management can boost CMP’s environmental performance—aligning with the ESG goals of semiconductor fabs.
Toward Collaborative Growth
Supply Chain Collaboration
Grinding material suppliers can partner with abrasive-free technology firms to co-develop compatible soft polishing pads, chemical formulations, or modular system components—extending rather than replacing grinding technologies.
Capital & Technology Synergies
Traditional grinding giants can invest in or acquire abrasive-free startups, safeguarding themselves from disruption while accelerating innovation and diversification.
Technological progress in semiconductor manufacturing never stands still. But shifts between old and new methods often involve fusion rather than outright replacement. The grinding industry must embrace change, reimagine itself within a “grinding-plus” model, and work alongside abrasive-free technologies to drive sustainable chip manufacturing forward.