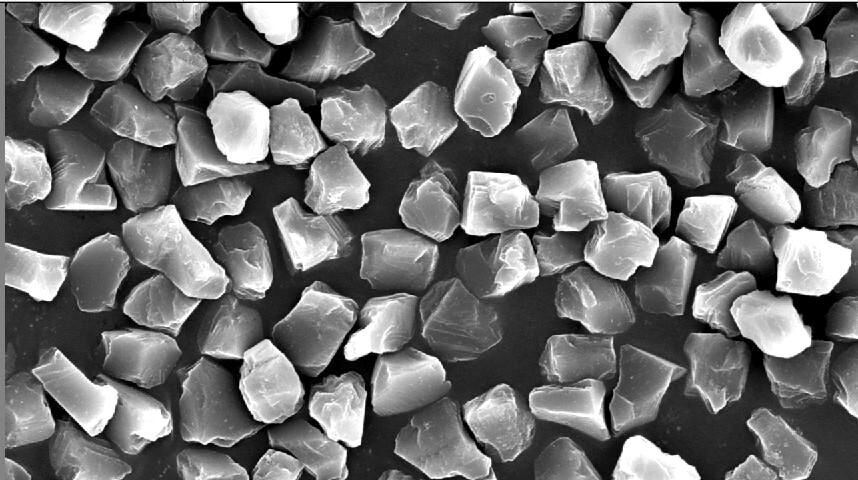
Table of Contents
- The Significant Meaning and Value of Developing Polycrystalline cBN
The emergence of cubic boron nitride (cBN) has brought immense benefits to the processing of hardened iron-based metals and alloys. However, synthesizing cBN requires ultra-high pressure and high-temperature conditions, which pose challenges due to the limitations of high-pressure equipment and synthesis technologies. Achieving high-quality, large-grain cBN single crystals is very difficult. Typically, the size of cBN single crystals is below 0.5 mm, and even those synthesized using the seed-temperature gradient method have sizes around 3 mm. Such small dimensions are only suitable for direct applications in abrasives and grinding wheels, making them too small for cutting tools.
Moreover, although single-crystal cubic boron nitride is very hard, its performance in certain processing applications remains less than ideal due to the effects of its crystal cleavage structure. Given the current inability to manufacture high-toughness single crystals large enough for cutting tools, is there a way to better address this issue?
This led to the development of polycrystalline cBN, sintered bodies, and composite materials. These technologies address the size issue of cBN, allowing for the production of bulk cBN materials with particle sizes ranging from 0.5 mm to 50 mm. Furthermore, since these materials have a polycrystalline structure, they do not exhibit cleavage issues, significantly enhancing the toughness of cBN materials. Consequently, the technology for polycrystalline sintered bodies and composites has flourished.
What are cBN polycrystalline materials and microcrystalline cBN?
cBN polycrystalline materials consist of many small cBN single crystals that are interconnected in a randomly oriented aggregate. Besides having the properties of single-crystal materials, the random orientation of single crystals within the aggregate overcomes the anisotropy of single-crystal materials, providing superior performance in terms of toughness.
Microcrystalline cBN is composed of numerous sub-micron-sized single crystals of cBN, with particle sizes ranging from 0.1 to 0.8 mm. In microcrystalline structures, the cleavage planes are randomly oriented and form a fairly dense structure, which exhibits high hardness and wear resistance against macro-cracking in all directions.
Microcrystalline cubic boron nitride was introduced by General Electric in the 1980s under the product brand name Borazon CBN550. Compared to single-crystal cubic boron nitride, this product has the following characteristics:
(1) The abrasive grains consist of numerous single-crystal cubic boron nitride particles smaller than 5 μm, avoiding the anisotropy of single crystals;
(2) Thermal stability reaches up to 1473 K;
(3) Multiple cutting edges lead to high processing efficiency and precision;
(4) Self-sharpening;
(5) Larger abrasive grain size;
(6) Thermal stability is still not less than that of single-crystal materials, reaching 1200°C;
(7) The multi-edged shape increases gripping power in the product, enhancing cutting edge and efficiency;
(8) The size of microcrystalline grains can exceed 0.5 mm, overcoming the limitations of synthesizing large-grain cBN due to high-pressure equipment.
General Electric has compared single-crystal and microcrystalline cubic boron nitride, finding that when grinding difficult-to-process alloys such as M-2, M-4, and T-15, selecting appropriate bonding agents and grain sizes allows microcrystalline cubic boron nitride to achieve grinding efficiencies typically twice that of Borazon CBN-ll.
Due to its superior characteristics compared to single crystals, microcrystalline cBN has found extensive applications in industrial processing.
When using cBN grinding wheels to grind low-carbon steel, soft alloy steel, and tough high-temperature resistant alloy steel, the resulting metal chips tend to be longer, wider, and thicker compared to those produced with cemented carbide. To continue cutting, it is necessary to clear the chips and dress the grinding wheel. Additionally, the presence of these metal chips can erode the bonding agents in the wheel, creating pits. If these pits are comparable in size to the abrasive grains, they can pull grains from the surface of the wheel, accelerating its wear. Reducing the grain size to avoid these phenomena would significantly decrease grinding efficiency, which is economically undesirable. The introduction and application of microcrystalline cBN can effectively resolve these issues. Overall, the larger grain size, higher grinding efficiency, and irregular shape of microcrystalline cBN enhance gripping power. Each single crystal within the microcrystalline structure has a small particle size, preventing the formation of long, stringy chips during processing, and ensuring that wear occurs on a smaller scale within the microcrystalline structure. This allows for high cutting efficiency and extended tool life when cutting the aforementioned materials, achieving an optimal balance.
Microcrystalline cBN also exhibits excellent thermal performance. Residual stresses often exist in cBN single-crystal abrasives, and these stresses can cause the crystal to fracture at around 700°C, impacting the product's lifespan. Experiments with microcrystalline cBN indicate that cBN550 abrasives retain their toughness even after exposure to high temperatures of 1200°C. This not only increases the product's lifespan due to the crystal's heat resistance but also allows for the use of high-temperature bonding agents in manufacturing, which is another crucial factor in extending product longevity.
- Manufacturing of Microcrystals
Microcrystals can be manufactured through two pathways: the sintering of hexagonal boron nitride (hBN) and cubic boron nitride (cBN). An economically feasible method involves the transformation of hBN with the participation of additives. The process flow is as follows: mix hBN with additives → synthesis → granulation → cleaning → screening → testing.
The hBN used for manufacturing microcrystals requires low impurity content, which can be achieved by treating hBN at approximately 2273 K to remove impurities. Additionally, high-purity boron nitride additives such as Mg₃N₂, Ca₃N₂, Li₃N, or AlN can be selected, with a suitable dosage that typically ranges from 3% to 10%; both excessive and insufficient amounts can affect the quality of the abrasive grains.
After uniformly mixing the treated hBN with additives, assembly occurs, with the synthesis temperature controlled between 1773 and 2273 K, pressure at 5-7 GPa, and synthesis time lasting 5-30 minutes. The resulting microcrystals are then crushed using a jaw crusher, with the gap between the jaw plates adjusted as needed to achieve different granule sizes, followed by cleaning and screening.
- Factors Affecting the Properties of Polycrystalline cBN
Using PcBN for high-speed and dry cutting can reduce processing costs. However, compared to traditional hard alloys and ceramic tools, the preparation and synthesis of PcBN tools are relatively challenging. PcBN tools must meet the following two requirements:
(1) The PcBN tool materials must be standardized to meet the needs of various material processing applications.
(2) While meeting the quality and consistency requirements for processed workpieces, the production and synthesis processes should be simplified as much as possible to reduce costs.
This section will introduce the influence on the performance of polycrystalline cubic boron nitride (PcBN) from aspects such as substrate selection, bonding agent selection, CBN grain size selection, and synthesis process selection.
3.1 Substrate Selection
Polycrystalline cubic boron nitride (PcBN) uses hard alloy as a substrate, on which a layer of cBN single crystal fine powder mixed with a binding agent is laid and then sintered through high temperature (1400-2600°C) and high pressure (7-9 GPa). Research on PcBN tools generally focuses on how to enhance the service life of the PcBN layer and provide an appropriate intermediate layer between the PcBN layer and the substrate, while less attention is given to the performance of the substrate itself. In fact, the substrate has a significant impact on the performance of PcBN. For example, microcracks inside the PcBN layer may propagate into the substrate during processing; if the substrate performs well, it can prevent crack propagation and thus improve tool longevity.
Common substrate materials are hard alloys, which are formed by sintering a mixture of WC, TiC, TaC particles and binding agents (Fe/Co/Ni). Their wear resistance improves with the reduction of grain size and cobalt content, while impact resistance increases with the enlargement of grain size and cobalt content. The desired hard alloy substrate can be obtained by adjusting the grain size of WC and cobalt content. In addition to focusing on the mechanical properties of the substrate, attention should also be paid to thermal properties, such as thermal conductivity and thermal fatigue resistance.
Experiments have shown that:
(1) Substrate materials with larger WC grain sizes exhibit higher thermal fatigue resistance.
(2) Thermal conductivity increases with larger grain sizes and reduced cobalt content.
(3) Substrates with coarse grains and high cobalt content show improved anti-friction properties and fracture toughness.
Therefore, to obtain a substrate material with good mechanical and thermal properties, the WC grain size should be maintained at 7-9 μm, with impurity content controlled below 0.01%. The cobalt content should be kept between 10% and 16%.
3.2 Selection of Bonding Agents
Due to the small particle size of single crystal cBN and the presence of easily cleavable cleavage planes, polycrystalline PcBN is predominantly used as cutting tools in industry. PcBN consists of numerous small, non-directional cBN single crystals and bonding agents. Depending on whether a bonding agent is included in the system, it can be classified as PcBN with bonding agents or pure PcBN. A dense boron oxide film on the surface of the cBN single crystals hinders the direct bonding of CBN grains, making it difficult to achieve high-strength pure PcBN. Therefore, various bonding materials need to be added during the polymerization process to enhance the connections between cBN grains.
Currently, there are three types of bonding agents for PcBN, both domestically and internationally.
3.2.1 Metal and Metal Alloy Bonding Agents
The selection of metal bonding agents should meet the performance requirements for cutting and processing PcBN tools.
First, the bonding agent elements should be chosen from Fe, Co, and Ni, with their content accounting for 40% to 50% of the bonding agent.
Second, bonding agents should be selected from Cr, Mo, W, La, Ce, Y, Nb, Ta, Zr, V, Hf, Al, Ti, with their content accounting for 50% to 60% of the bonding agent's mass.
Third, trace alloy elements should be selected from C, Mg, S, Si, Cu, P, B, N, Sn. The principle of selection is to ensure firm bonding of the cBN grains while forming ultra-heat-resistant alloys to guarantee the high-temperature performance of the PcBN tools (with Ti alloys being a better choice). Furthermore, to ensure high hardness and wear resistance of the PcBN tools, the content of cBN should not be lower than 70%, preferably between 75% and 85%. The average grain size of cBN should be comparable to that of the substrate, around 9 μm. Additionally, no more than 5% of rare earth oxides can be added to the bonding agent to enhance the wear resistance of PcBN.
3.2.2 Ceramic Bonding Agents
Ceramic bonding agents typically include metal oxides and carbides, borides, nitrides, and oxides of group IV, V, and VI elements in the periodic table, such as Al₂O₃, TiN, TiC, TiCN, AlN, AlB₂, AlCN, etc. While ceramic phases are heat-resistant and have high hardness, they are also significantly brittle. Toughening methods can be used to improve the impact resistance of PcBN tools primarily based on ceramic bonding agents, such as increasing whiskers, phase transformation toughening, and adding trace rare earth elements. Among these, ZrO₂ phase transformation toughening and Si₃N₄, SiC whiskers toughening are considered effective methods.
According to the toughening mechanism of ceramic whiskers, whiskers should be selected with elastic moduli and coefficients of thermal expansion less than or equal to those of the substrate material. Experiments have shown that the elastic moduli and thermal expansion coefficients of SiC whiskers and Si₃N₄ whiskers are relatively close to those of cBN, making them ideal toughening materials for PcBN tools.
3.2.3 Metal-Ceramic Mixed Bonding Agents
PcBN synthesized using metal and its alloy-based bonding agents exhibits good toughness; however, under high-temperature and high-pressure conditions, the bonding agent tends to soften, resulting in low hardness and poor wear resistance. Pure ceramic bonding agents can resolve these issues, but the toughness and impact resistance of the synthesized PcBN remain poor, leading to chipping and a short tool lifespan during use. Mixed bonding agents composed of ceramics and metals can compensate for the shortcomings of both types.
When synthesizing PcBN with a metal-ceramic bonding agent, it has been found that a formula of Al + Ni + Ti(C,N) + Co results in the best wear resistance and impact toughness. During the sintering process, Ni and Co are in a molten state, generating new phases that encapsulate Ti(C,N), enhancing the bonding strength of PcBN. The percentage content of Co and Ti(C,N) significantly influences the performance of PcBN. When the percentage of Co increases from 3% to 5%, the wear ratio increases by about 19%, the impact toughness rises by approximately 30%, and hardness increases by around 14%. When the percentage of Ti(C,N) rises from 1.5% to 3%, the wear ratio increases by about 6%, and the bending strength increases by approximately 12%.
XRD studies have shown that Co remains completely in a molten state during sintering and reacts chemically with cBN to generate new phases such as Co₀.₄₇N and Co₂B, which encapsulate Ti(C,N) and create a strong interfacial bond, forming a dense network structure that enhances the density of the sintered body. A small amount of WC can be added to form a solid solution with TiC and TiN, improving the overall performance of PcBN, but the quantity should not be excessive.
3.4 Selection of cBN Grain Size
Research indicates that a mixed particle size of cBN performs better than a single particle size, and a wider range of mixed particle sizes is preferable to a narrow range. This is because the size of cBN particles directly affects the toughness of PcBN: larger particle sizes enhance resistance to mechanical wear but reduce damage resistance, leading to poorer sharpness of the cutting tools produced. Mixed particle sizes can effectively improve the packing state of the grains; a higher packing density results in more complete crystallization during synthesis.
3.5 Selection of Synthesis Process
Heating methods can include direct electric heating or spark plasma sintering (SPS), also known as pulsed electric current sintering (PECS) and field-assisted sintering technique (FAST). This is a new technology for rapid, low-temperature, energy-efficient, and environmentally friendly material preparation. In this technique, direct current pulses are passed between the processing particles, generating Joule heat within the particles, leading to temperature differences of hundreds to thousands of degrees, facilitating the formation, expansion, and densification of sintering necks. The energy consumption is only about 1/5 to 1/3 of that of traditional sintering processes (such as pressureless sintering, hot pressing, and hot isostatic pressing).
SPS technology has unparalleled advantages over hot isostatic pressing:
(1) Rapid sintering (generally, densification takes only 0-10 minutes, while hot pressing and hot isostatic pressing require 120-300 minutes);
(2) Lower sintering temperatures (compared to hot pressing and hot isostatic pressing, sintering temperatures can be reduced by 200-300°C);
(3) Unique sintering mechanism (internal heating of the powder with electric and magnetic field effects);
(4) Simple and convenient operation, unlike hot isostatic pressing, which requires highly skilled workers and mold technology;
(5) Small equipment footprint, high automation, and short process flow;
(6) No need for powder preforming; direct sintering into dense bodies is possible, making it particularly suitable for the preparation of special powders like spherical, amorphous, or nanoscale materials;
(7) Through special design of molds, it can easily achieve ultra-high pressure sintering and temperature gradient sintering, making SPS technology very suitable for the sintering of PcBN tool materials.
- Applications in Technical Fields
Isotropic PcBN (polycrystalline cubic boron nitride) is an ideal tool material and is widely used in automotive, aerospace, and aviation industries. PcBN, made with cBN micropowder as a framework and a binder as a bonding material, is a composite material sintered under ultra-high pressure and temperature conditions. It overcomes the shortcomings of machining single crystal cBN. Liu et al. analyzed the grinding effects of different bonding agents on PcBN tools and concluded that ceramic-based PcBN tools are the most suitable.
PcBN is a new type of high-performance superhard tool material that emerged in the 1970s, opening up broad application prospects for modern machining technologies such as hard cutting, dry cutting, and green machining. It has become the best tool material for high-speed, efficient, and precise processing of black metals. For PcBN tools used in high-speed hard cutting, not only is good heat resistance (thermal stability and oxidation resistance) required, but it is also crucial that PcBN tool materials exhibit good high-temperature mechanical properties, thermal shock resistance, long tool life, and high safety and reliability.
In addition to the material performance itself, the geometric angle design of PcBN tool materials is also critical. The cutting performance of PcBN tools mainly includes tool life and the quality of the machined surface of the workpiece. Reasonable structural parameters and optimal cutting process conditions significantly affect metal deformation during cutting, cutting force, cutting temperature, and tool wear, improving production efficiency while ensuring processing quality and tool life, thereby reducing production costs for enterprises.
The German Becker Diamond Company has introduced a PcBN indexable insert, with a PcBN content of 95%, that can increase tool life by 30%-50% when turning materials such as sintered metals, cast iron, and titanium alloys. This insert can also be used for machining particularly hard and tough materials (such as Stellite 20).
PcBN tools are applied in dry cutting, utilizing advanced cutting processes such as turning instead of grinding, which not only saves equipment investment and improves productivity but also significantly increases flexibility in the processing workflow. Additionally, due to rising labor costs and environmental protection requirements in the 21st century, there is significant importance in promoting the use of PcBN tools to fully exploit their potential. Through continuous in-depth research on the cutting process and mechanism of PcBN tools, their importance is expected to grow even more.